Recognizing that access to testing facilities is a key enabler of wind technology validation and commercialization, the Wind Energy Technologies Office funds and works with partners on the development of testing facilities that support research and certification of wind turbine technologies at the component, turbine, and wind plant levels.
Full-scale, accredited test facilities and trained engineers capable of developing test methods and conducting full-scale tests are in high demand, but these facilities can be cost-prohibitive for any single company to build and operate. The federal government to date has provided component and system test facilities that industry can use to validate designs prior to large-scale deployment.
U.S. Department of Energy facilities span the United States and offer wind research capabilities to meet industry needs. For more information, check out our Wind Energy Facilities Guide which highlights the testing facilities that make it possible for wind technology companies and inventors to validate and commercialize their technologies.
U.S. Department of Energy facilities span the United States and offer wind energy research capabilities to meet industry needs. For more information, check out our Wind Energy Facilities Guide, which highlights the testing facilities that make it possible for wind energy technology companies and inventors to validate and commercialize their technologies.
This has been especially true for wind turbine blades and drivetrains, where Department of Energy test facilities have been used to perform highly accelerated life testing. These test facilities support office collaboration on industry codes and standards development, including components and system design requirements, testing requirements, measurement techniques (load, power quality, and acoustics), modeling techniques, safety concerns, and conformity testing and certification. To stay ahead of wind turbine test facility needs, the office has made important, timely funding in building these important test facilities. These testing facilities are geographically diverse, located in key wind energy regions, and possess unique testing capabilities that allow the Department of Energy to usher in new and innovative generations of wind energy technology.
For additional information on these and other testing-related projects funded by the Wind Energy Technologies Office, view the office's research and development projects map and select Program Area: Testing.
Component Testing and Certification
According to the American Wind Energy Association, there are roughly 8,000 component parts in a utility-scale wind turbine, including the blades, rotors, generator, or other parts located inside the nacelle.
The Wind Energy Technologies Office funding works to create partnerships for the creation of wind technology testing facilities, in order to help industry develop and manufacture the most cost-effective, reliable, and innovative wind turbine components. Research, testing, and certification of these wind turbine components are important steps in validating wind turbine component design, performance, and adherence to safety standards.
Wind Technology Testing Center (Boston, Massachusetts)
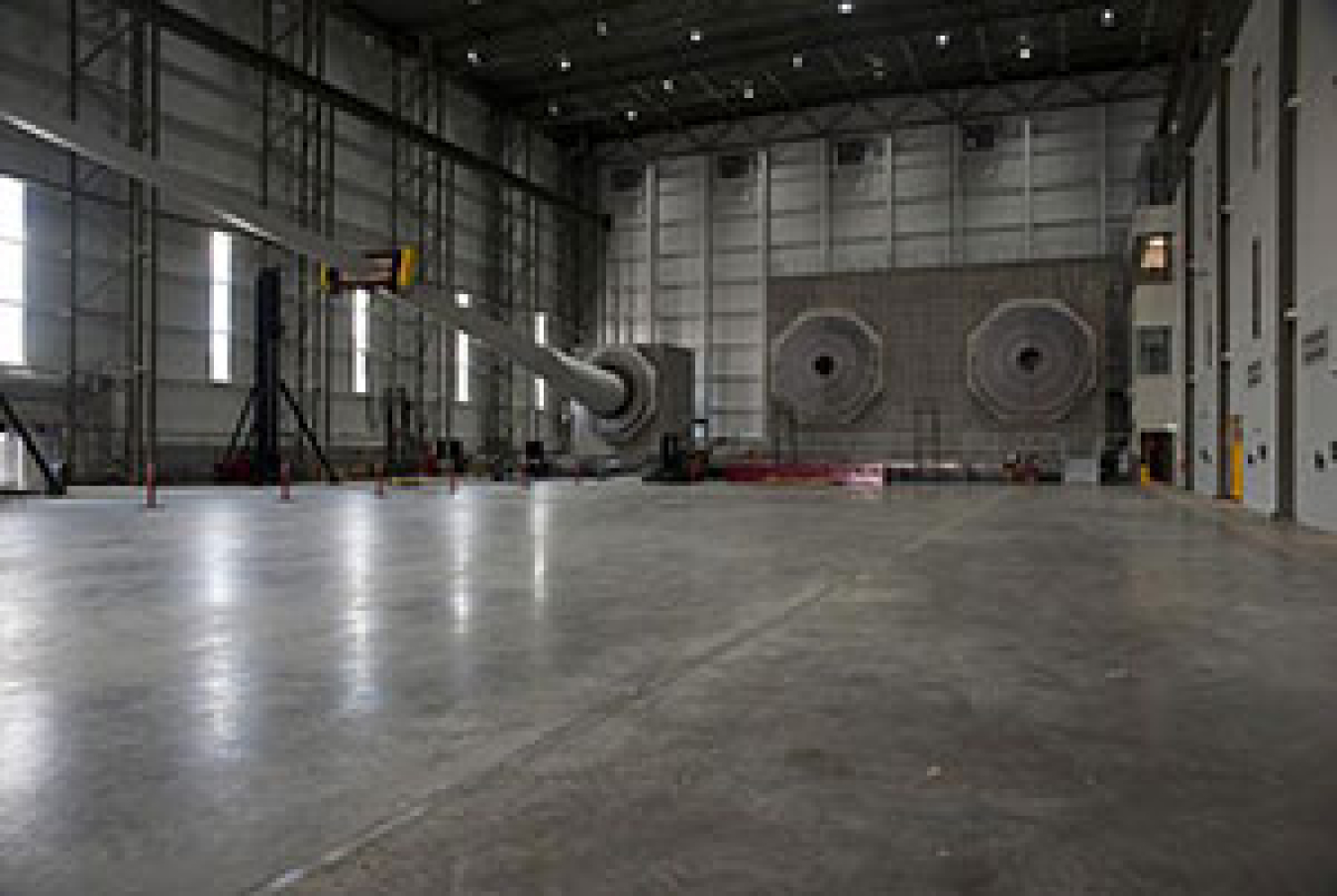
The Wind Technology Testing Center, located near Boston, Massachusetts, has enough space to test up to three blades simultaneously.
Located near the Port Authority in Boston Harbor, the Wind Technology Testing Center is the first commercial large-blade testing facility in the nation and allows for testing of blades as long as 300 feet (90 meters). With close proximity to substantial offshore wind resources and a 1,200-foot (360-meter) dock for handling blades, the center is ideally located to support the emerging U.S. offshore wind industry. Testing and certifying large blades—a key component of large-scale wind turbines—will enable the development of offshore wind power facilities, which generally use higher-capacity turbines with longer blades to accommodate stronger offshore wind resources. Certifying larger blades and higher-rated turbines allows offshore developers to use fewer turbines, reducing operations and maintenance costs.
A joint project between the Wind Energy Technologies Office, the Massachusetts Renewable Energy Center and the National Renewable Energy Laboratory, the Wind Technology Testing Center facility is accredited by the American Association for Laboratory Accreditation (A2LA) to test wind turbine blades to International Energy Commission (IEC) standards. The facility is equipped with three test stands, and specific testing capabilities include blade materials testing, hands-on workforce training, and a full suite of static and fatigue tests to the IEC61400-23 standard. Since the center opened in May 2011, it has performed blade testing on a variety of 160-foot (50-meter) wind turbine blades to support the industry in improving reliability and reducing cost of energy. The Wind Energy Technologies Office contributed $24.7 million to the construction of the Wind Technology Testing Center, with funding provided under the American Recovery and Reinvestment Act.
Clemson Drivetrain Testing Facility (North Charleston, South Carolina)
A wind turbine test bed located within the Clemson University SCE&G Energy Innovation Center, located near Charleston, South Carolina. The test stand is capable of testing drivetrains up to 7.5 MW in size.
Funded in part by a $44.5 million Wind Energy Technologies Office grant under the American Recovery and Reinvestment Act, the Clemson University SCE&G Energy Innovation Center is aimed at boosting American innovation and competiveness in manufacturing wind turbine drivetrains. Located at a converted Navy warehouse, this center will test the machinery that converts wind energy to electricity, allowing engineers to perform highly accelerated lifetime testing, that is, to simulate 20 years' worth of wear and tear on large drivetrains in only a few months.
The facility houses two testing bays — one dynamometer rated at 7.5 megawatts (MW) and another dynamometer rated at 15 MW, making it the only facility of this size in the world. The testing facility also houses a grid simulator, funded under a separate Wind Energy Technologies Office grant, which allows for testing of wind turbine generators' compatibility with 50 or 60 hertz (Hz) electrical transmission grids. The grid simulator will also mimic real-world circumstances—such as wide-area power disruptions, frequency fluctuations, voltage drops, cascading accidents, and cyber or physical attacks—to determine the effects of the wind turbine on the utility grid, and the grid on the wind turbine.
National Wind Technology Center (Boulder, Colorado)
The National Wind Technology Center is located at the base of the foothills just south of Boulder, Colorado, and is the nation's premier wind energy technology research facility.
Facilities at the National Renewable Energy Laboratory's National Wind Technology Center (NWTC) support the testing of wind turbines and components with dynamometers that range in size from 400 watts to 5 MW, a grid simulator, blade testing facilities, and full-scale turbine testing pads. NWTC's engineers provide wind industry manufacturers, developers, and operators with testing to verify the performance and reliability of blades, turbines, and other components.
NWTC staff conducts tests both on components in laboratory environments and on turbines in the field to produce data that can be used to certify and validate turbine designs. Since 1993, this testing facility has helped both private industry and public researchers and academics drive new wind technology development, from more efficient blades up to 160 feet (50 meters) in length to stronger, more durable drivetrains.
Small Wind Turbine Testing and Certification
The recent growth and development of the international small wind industry has seen a large number of new products enter the U.S. market without a framework for verifying manufacturer claims about turbine performance, reliability, noise, and safety. In response, the Wind Energy Technologies Office supported the development of technical standards that can now be used voluntarily to test small wind turbines to performance and safety criteria, and supported the establishment of four small wind turbine regional testing centers and the Small Wind Certification Council, which provides accredited third-party verification of test results in accordance with internationally adopted technical standards for testing.
The Wind Energy Technologies Office views small wind turbine certification as a way to provide manufacturers with the parameters for communicating transparent and credible information to consumers, utilities, lenders, and policymakers about the safety, performance, and durability of small wind turbines. A unified list of certified small wind turbines is maintained by the Renewable Energy States Alliance.
Wind Plant Characterization
Improving the performance of an individual wind turbine and its components is just one piece of the puzzle for reducing the cost of wind energy. Another important piece is improving wind plant performance by analyzing how wind turbines interact with one another in a wind plant or wind farm. Together with industry partners and national labs, the Wind Energy Technologies Office is working to build the wind plant of the future.
Scaled Wind Farm Technology Facility (Lubbock, Texas)
The result of a research partnership by the Wind Energy Technologies Office and Sandia National Laboratories, with funding by Vestas, Texas Tech University (TTU), Group NIRE and ABB, the Scaled Wind Farm Technology (SWiFT) site, located at TTU's Reese Technology Center in Lubbock, enables rapid, cost-effective testing and development of transformative wind energy technologies. Supported by a $5.06 million Wind Energy Technologies Office funding, the SWiFT site performs at the highest quality of accredited research testing for both collaborative and private research projects with industrial, governmental, and academic partners.
SWiFT's primary objectives are to reduce power losses and damage caused by turbine-turbine interaction, enhance energy capture and damage-mitigation potential of advanced rotors, and improve the validity of advanced simulation models used to deploy advanced wind technologies. The initial SWiFT site is comprised of three heavily-instrumented, research-scale wind turbines that can operate together to simulate a wind farm or independently from one another for different test scenarios. In addition, multiple anemometer towers are located on-site and TTU has a range of additional instrumentation available for researchers. In the future, the SWiFT Facility could accommodate up to seven additional turbines.
Take a virtual tour of the SWiFT site or watch a time-lapse.
Wind Testing and Certification News
-
The American WAKE experimeNt (AWAKEN) is compiling the world’s largest and most comprehensive dataset on wind energy atmospheric phenomena, detailing how wind and surrounding air particles interact with wind turbines and wind farms.
-
With three recently installed small wind turbines at the Flatirons Campus in Colorado, WETO is poised to take the next step in proving and improving the next generation of distributed wind technologies.
-
Thanks to funding from the Wind Energy Technologies Office, the Massachusetts Renewable Energy Center’s Wind Technology Testing Center (WTTC) is testing next-generation wind turbine blades.
-
With support from the U.S. Department of Energy’s Wind Energy Technologies Office, the National Renewable Energy Laboratory is helping grid operators and equipment manufacturers successfully adapt to the energy transition using the Grid Impedance Scan Tool.
-
While studying mechanical engineering at the University of Texas in Austin, Paquette became interested in structural components and composite materials. Although he originally planned to pursue work in the aerospace industry, he jumped at the opportunity to work at Sandia on wind turbine blades—the largest composite structures in the world.
-
The Wind Energy Technologies Office (WETO) has funded the blade and drivetrain testing facilities since the 1990s, providing crucial knowledge and expertise to the ongoing expansion of commercial wind power—both domestically and globally.
-
The DOE-NASA Mod-Series Wind Turbine Program precedes the modern wind energy industry in the United States. For over two decades, with five distinct models built, the program helped shape a cost-competitive wind energy industry through funding and R&D.
-
A new report for the International Energy Agency Wind Technology Collaboration Programme summarizes the findings of a meeting of global wind energy experts who identify the five Grand Challenges
-
A WETO-funded partnership between General Electric, Sandia National Laboratories, and the National Renewable Energy Laboratory is enhancing data collection efforts to improve the accuracy of wind industry simulation tools.
-
Regional wind data from around the U.S. helps improve a national weather forecasting model, which allows utility companies to better plan for windy days.
Stay informed by receiving the latest wind energy research and development activities, news, events, and updates.