The United States wind industry is progressing from a period of experimentation and development to a period of wide scale demonstration and actualization, which is leading to advancements in infrastructure. As the wind industry continues to grow, logistical constraints must be identified and resolved in order to prevent bottlenecking in the supply chain and installation process. U.S. manufacturers are working together to overcome many of the challenges facing the industry as a whole.
Infrastructure and Logistical Challenges
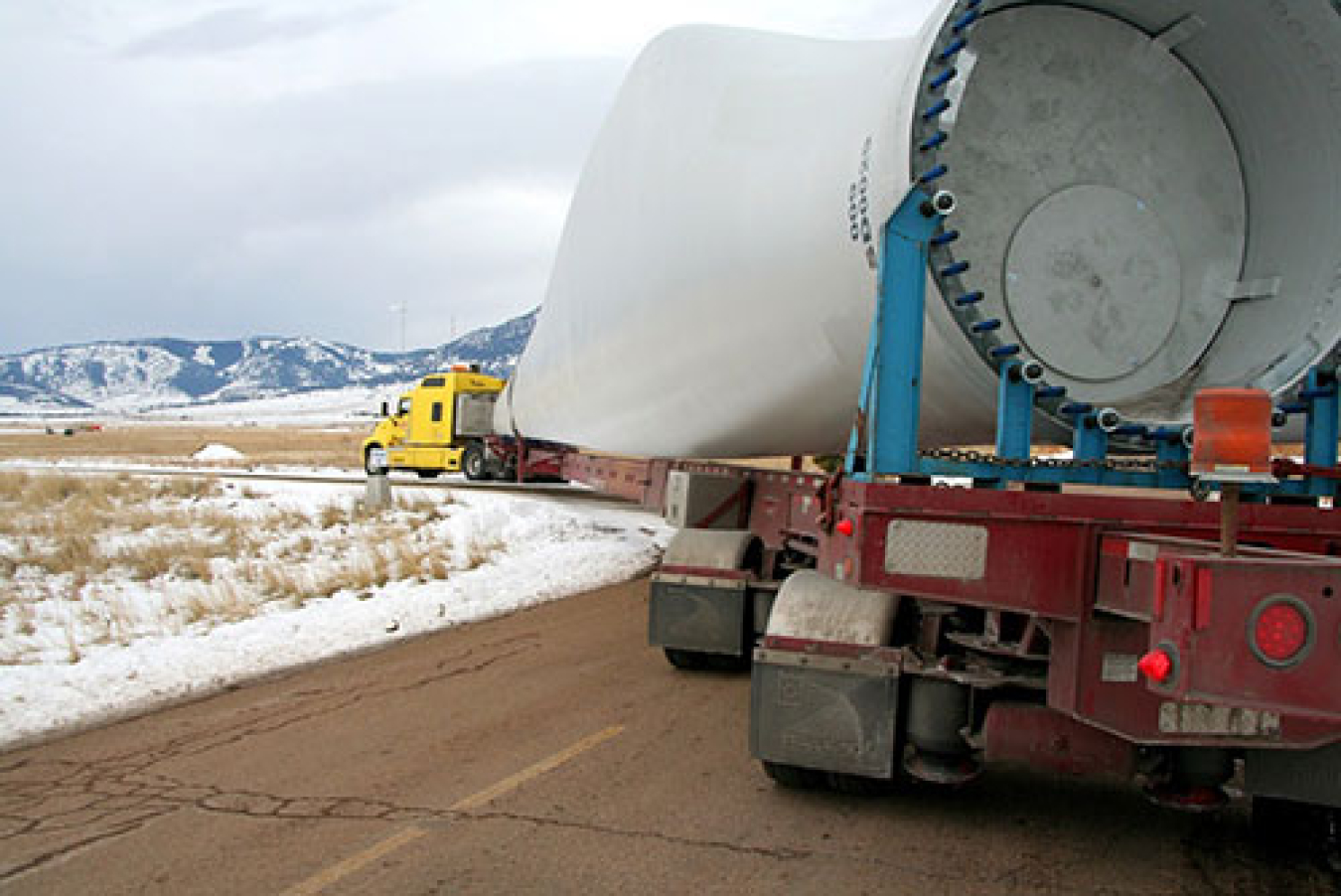
The logistics of delivering and installing increasingly large wind turbine components is just one issue that requires attention if the U.S. is to meet 20 percent of its electricity needs with wind power by 2030. Image from NREL/PIX 16178
The infrastructure that supports the growing wind industry encompasses each and every part of the manufacturing and turbine installation process. This includes the selection of a turbine site; selecting the appropriate turbine design; acquiring all of the materials needed for production and fabrication; manufacturing each component; transporting sizeable components to installation sites; installing turbine components; connecting the turbine to the appropriate electrical grid; and maintaining each component throughout the lifetime of the turbine. Streamlining this process will bring more affordable wind energy to consumers across the country.
- One of the primary challenges facing the wind industry is the sheer size and dimensions of wind turbine components. Since components typically require special logistical handling throughout transportation, manufacturing is best completed locally.
- While the towers that support wind turbines extend high into the sky, the width of a turbine tower is also a significant factor to consider. The transportation of tower components is often obstructed when the diameter of components is unable to fit under highway overpasses or bridges.
- Manufacturing and transporting turbine blades that can reach hundreds of feet in length is no easy process. Once fully constructed, a blade cannot be bent or folded, limiting both the route a truck can take and the radius of turns that it can make, often making elongated routes necessary to avoid urban roadblocks.
- The U.S. Department of Energy's Big Adaptive Rotor project seeks to overcome transportation challenges associated with the creation of the giant, land-based turbines of the future by exploring innovations like highly flexible blades that simultaneously boost wind energy capture while resolving transportation challenges of moving giant wind blades by rail.
Wind Turbine Tower Heights
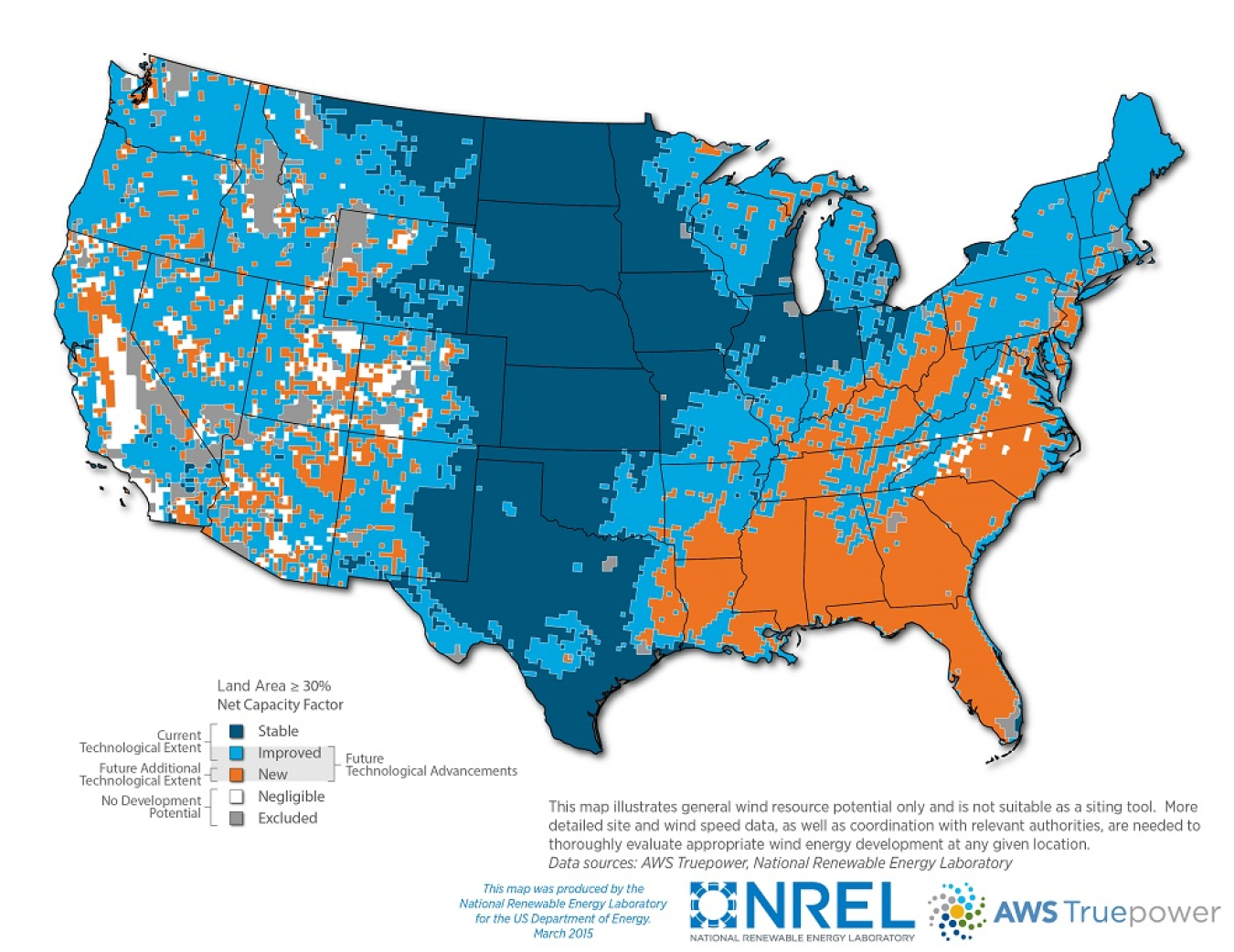
Expanded area of potential wind energy deployment resulting from increasing hub height to 140 meters. Image from NREL
In the northeastern, southeastern, and western United States, wind conditions near the ground are often low or turbulent, limiting the amount of electricity generated from wind energy. Today's utility-scale wind turbines average 82 meter hub heights, but taller wind turbines could take advantage of the stronger, more consistent winds available at greater heights, increasing the number of locations that can cost-effectively produce renewable wind energy.
In fact, the Energy Department's report, Enabling Wind Power Nationwide, shows that the key to unlocking wind energy’s potential in all 50 states is to access the stronger and more consistent winds found at increased heights above the ground. Continued technology advancements have the potential to unlock wind energy across an additional 700,000 square miles—or about one-fifth of the United States—and provide the opportunity for wind power to expand throughout the country. Unlocking this potential will require new manufacturing or installation techniques to address the transportation and logistics challenges associated with large towers.