It may look like ordinary farm equipment, but take a second look. This innovative machinery was developed with Energy Department funding to help biofuels become more affordable.
Office of Energy Efficiency & Renewable Energy
March 17, 2015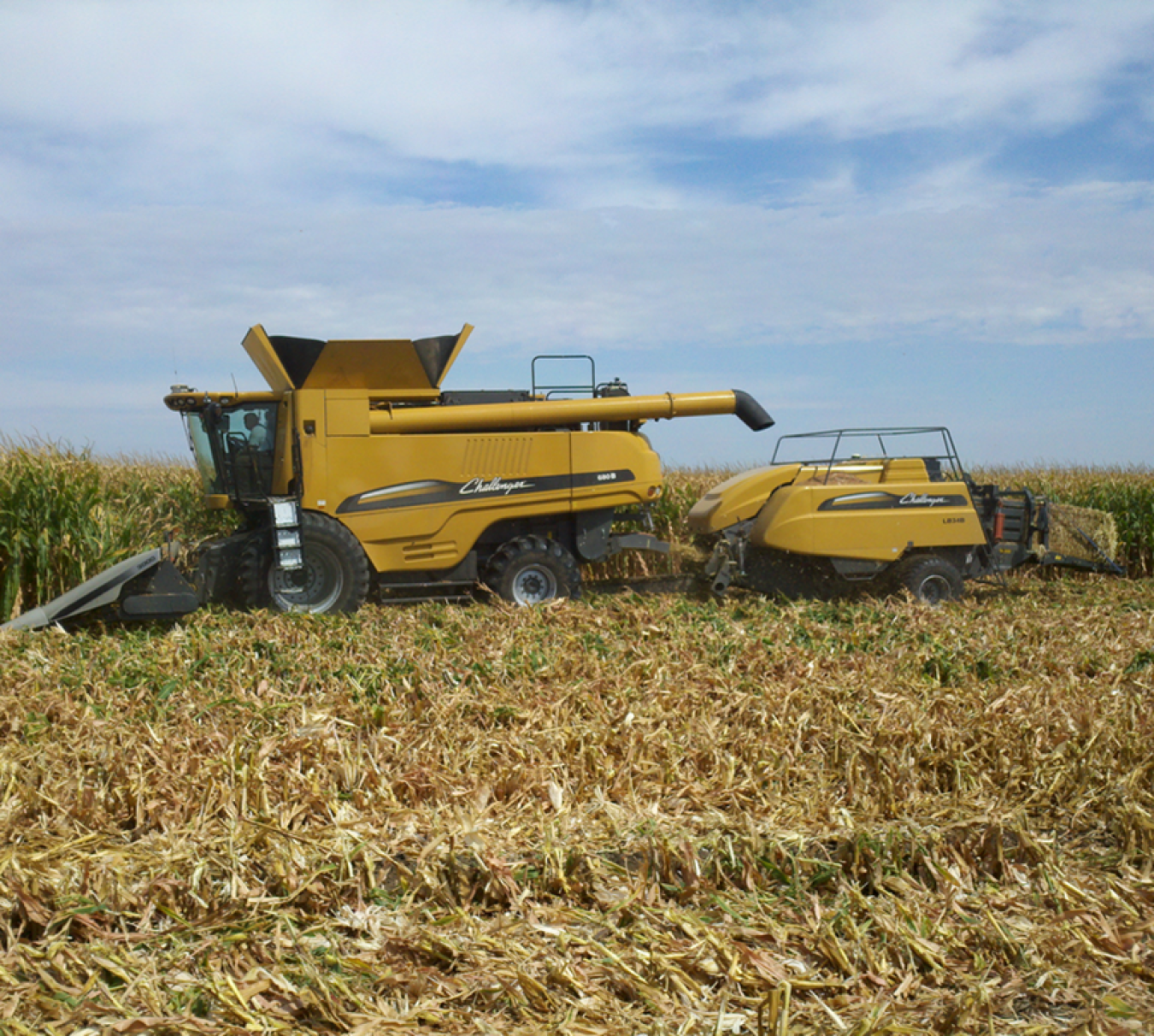
AGCO Project: AGCO Corporation’s Single-Pass Combination Harvester
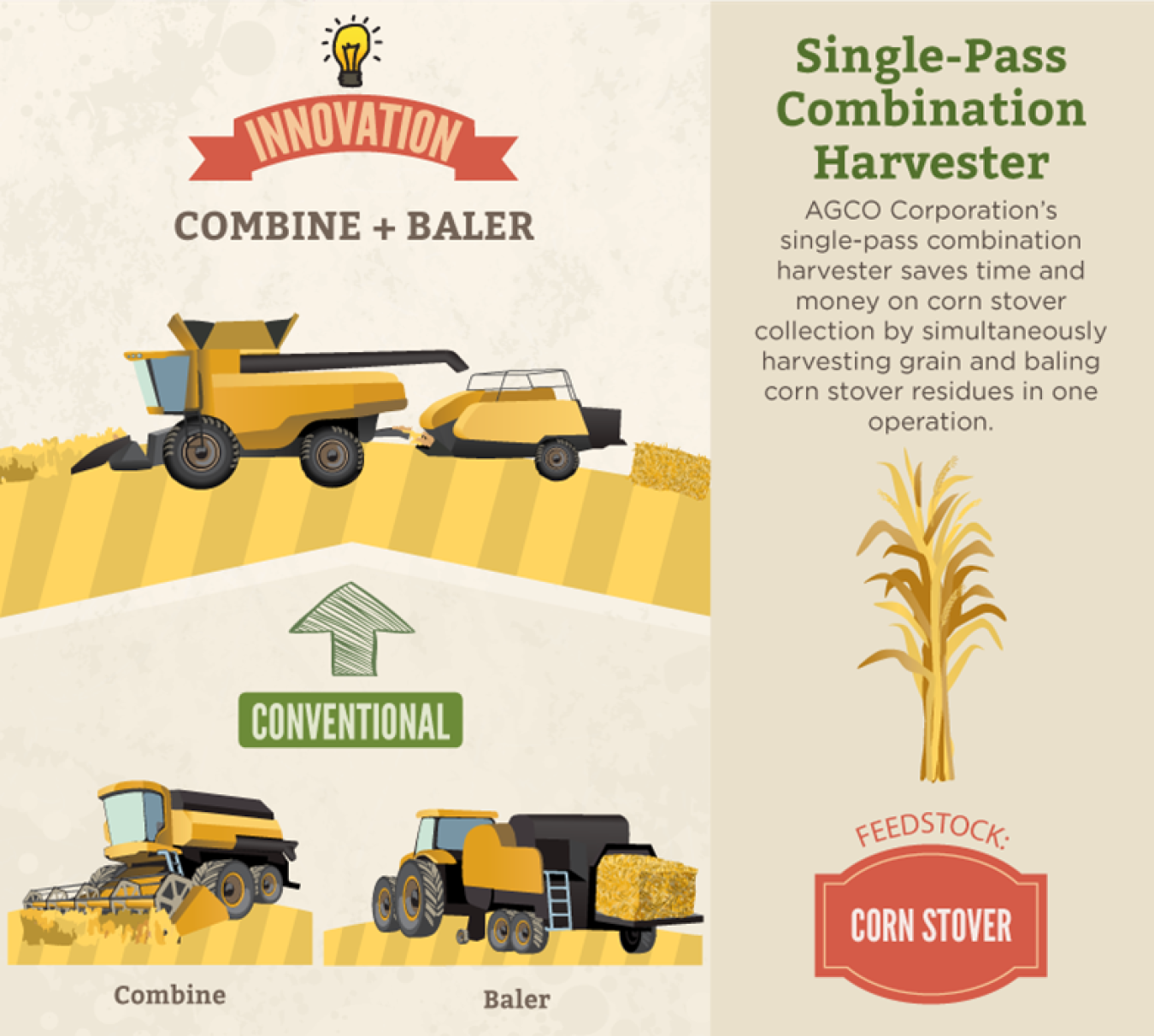
AGCO’s project also included the Stinger Advanced Load Securing System, which significantly reduces truck loading time and makes the strapping down operation much safer for the truck operator. These technologies reduced logistics costs by $14.79/dry ton feedstock, from $51.54/dry ton to as low as $36.75/dry ton (a 29% cost reduction).
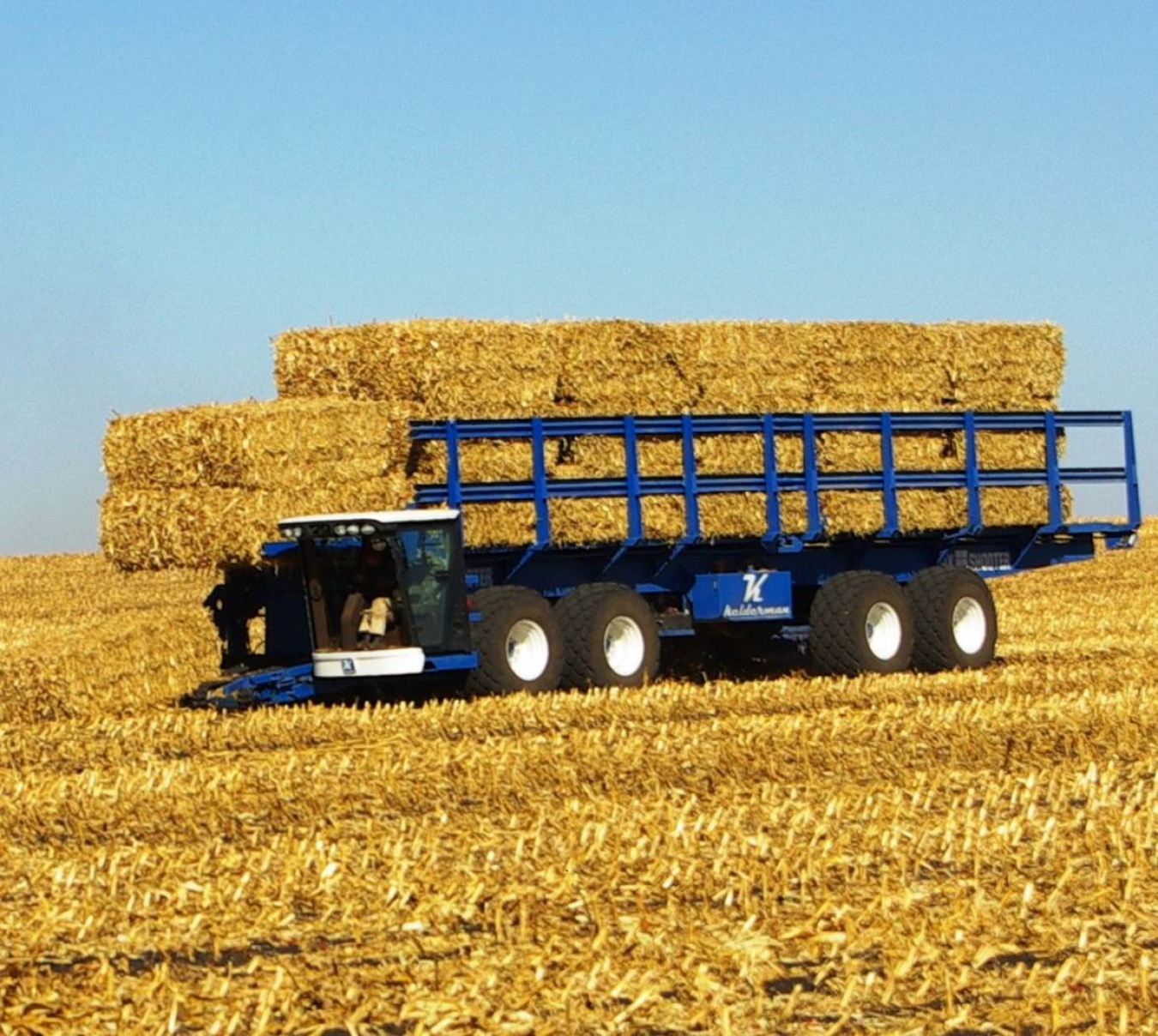
FDC Enterprises Project: Kelderman Manufacturing’s Self-Propelled Bale Picking Truck
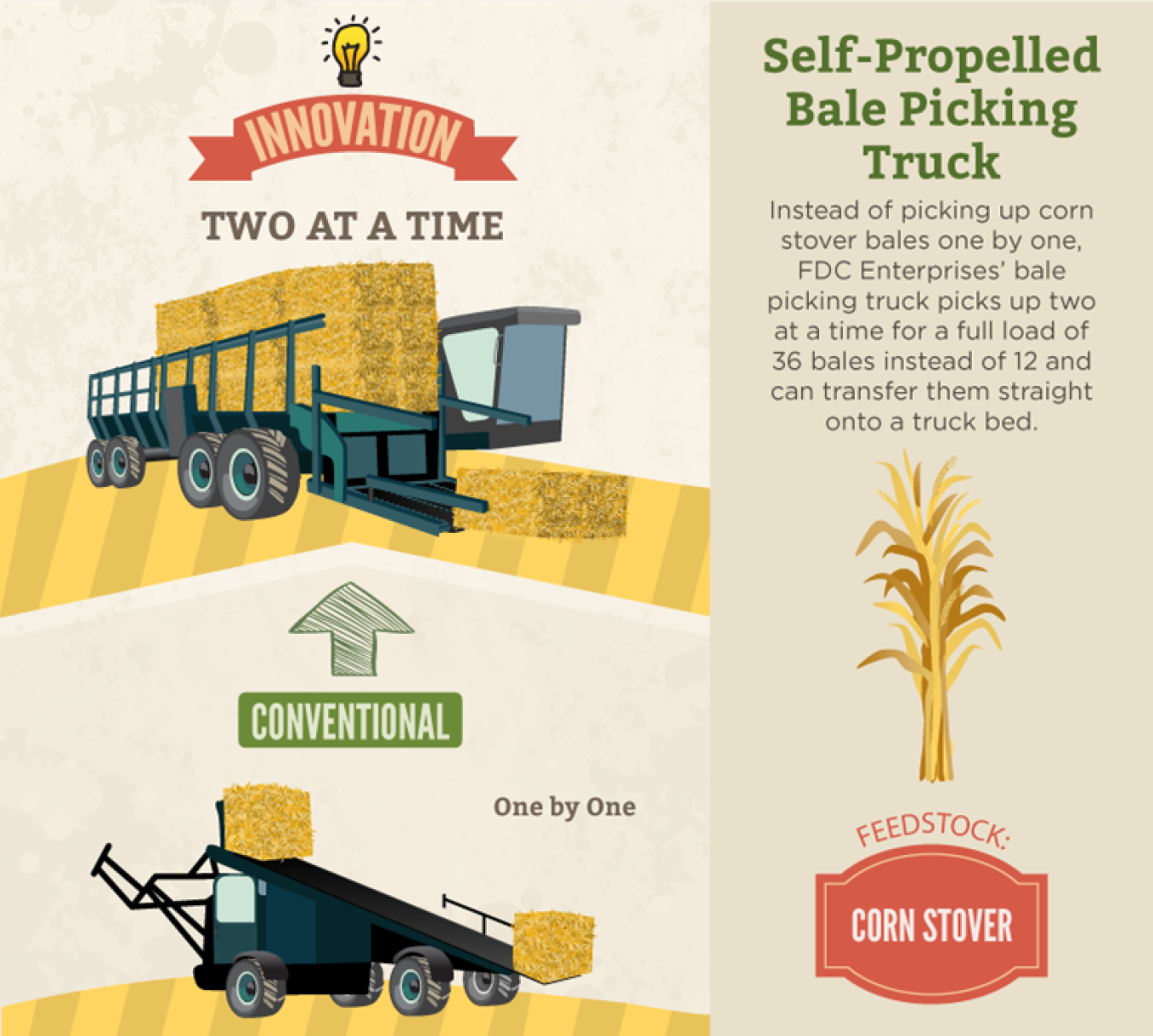
FDC Enterprise’s project also included a modified Allied-Freeman self-propelled baler with front-mounted rakes and the Kelderman Manufacturing Self-Loading/Unloading Trailer, which can accept an entire trailer load of bales directly from the bale pick-up truck. The three components work together in a system to efficiently harvest, package, and transport corn stover. These technologies could reduce logistics costs by $13/dry ton feedstock, from $51/dry ton to as low as $38/dry ton (25% cost reduction).

TennEra Project: TennEra’s Switchgrass Storage System
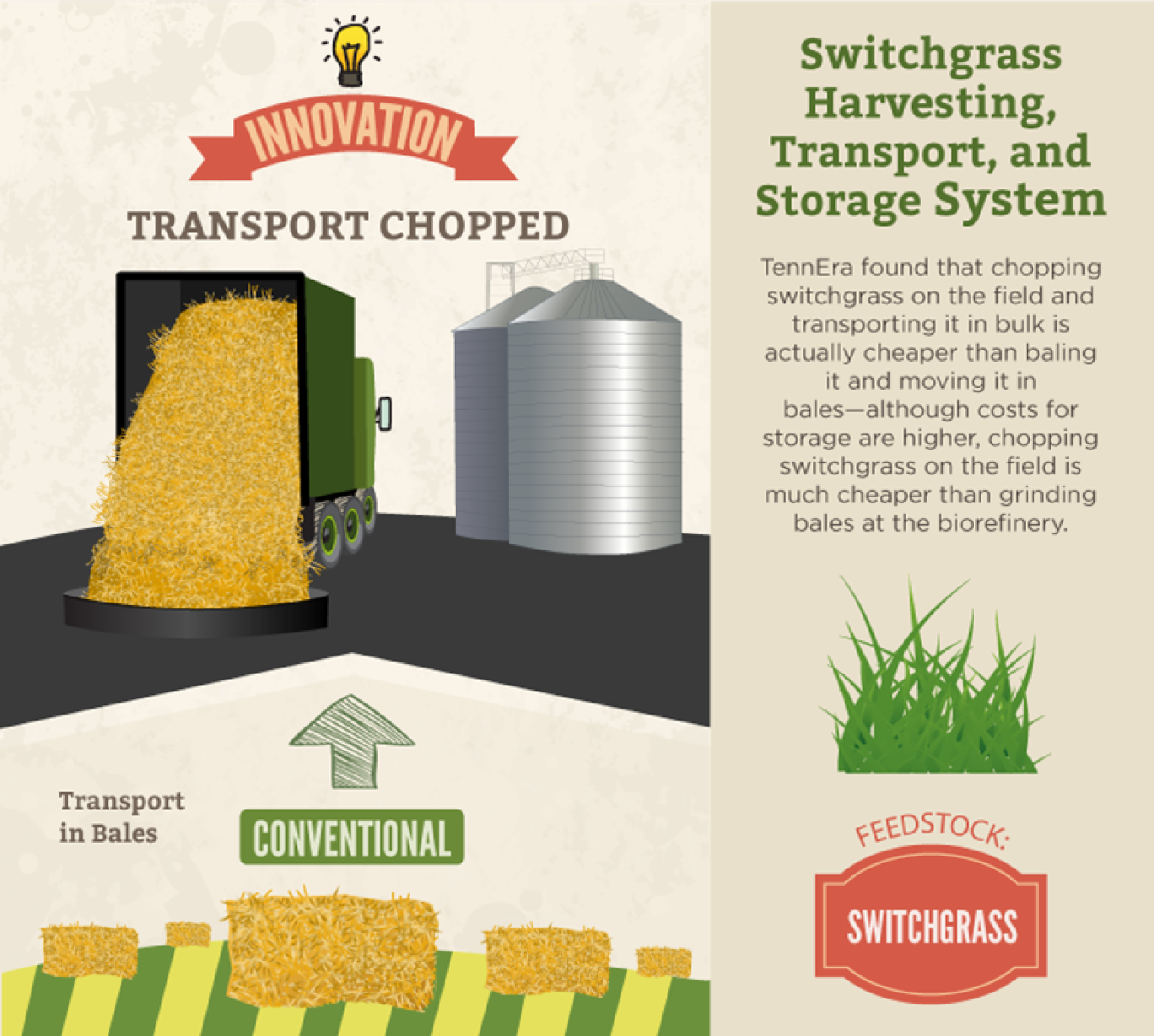
TennEra’s project is an entire innovative system that harvests and transports chopped switchgrass in bulk, using conventional machinery, including a self-propelled forage chopper in the field, windrowing equipment, and trucks and trailers for transport. Original equipment manufacturers included Marathon Equipment and Laidig Systems. These technologies reduced logistics costs by $4.04/dry ton feedstock, from $56.38/dry ton to as low as $52.34/dry ton (7% cost reduction).
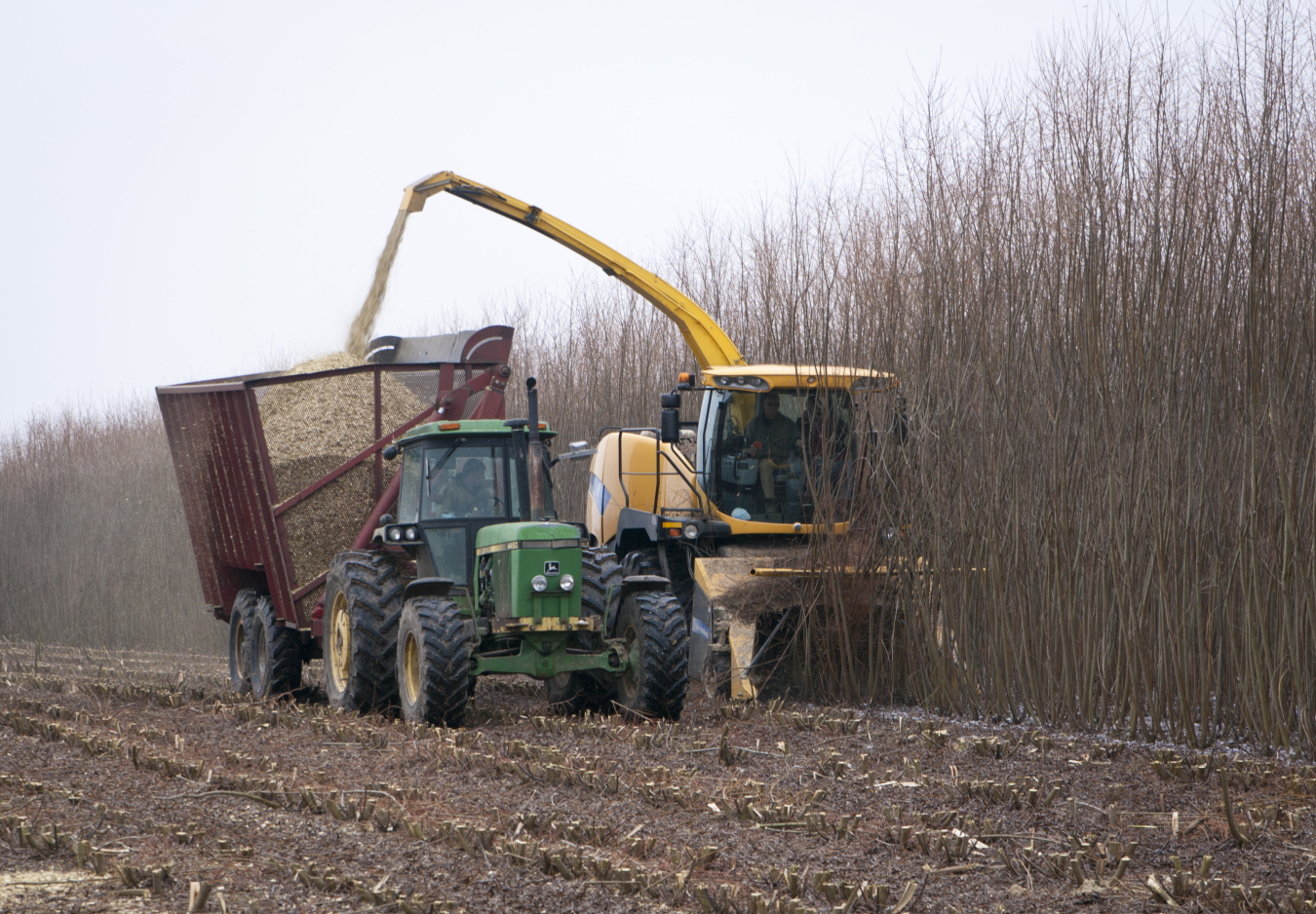
State University of New York College of Environmental Science and Forestry (SUNY-ESF) Project: The New Holland Forage Harvester fitted with the Short Rotation Woody Crop Coppice Header
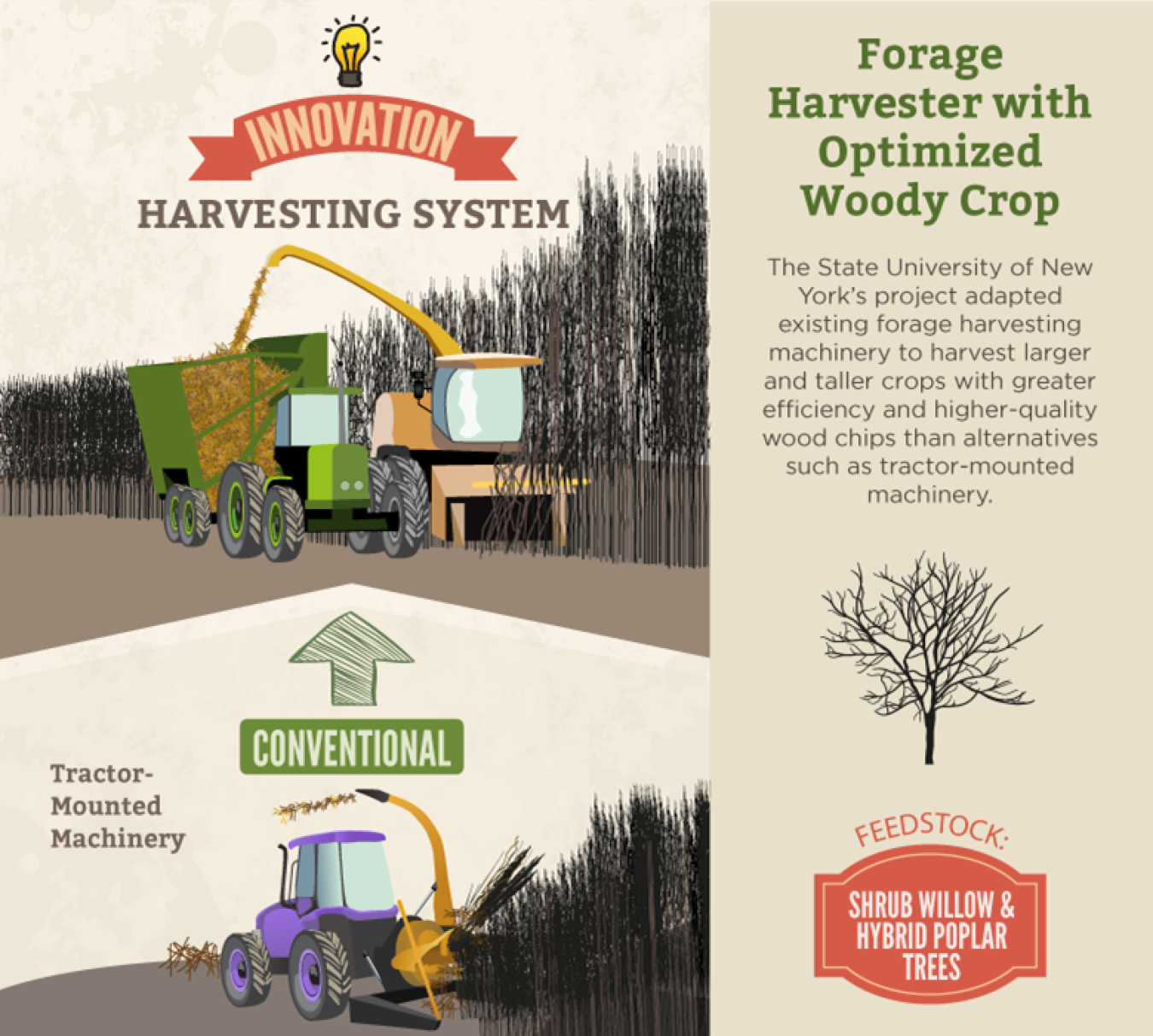
The State University of New York College of Environmental Science and Forestry (SUNY-ESF)’s project developed and demonstrated the short rotation woody crop coppice header that can be easily mounted and dismounted on this existing, commercially available New Holland forage harvest. These technologies reduced logistics costs by $17.49/dry ton feedstock, from $51.83/dry ton to as low as $34.34/dry ton (34% cost reduction).
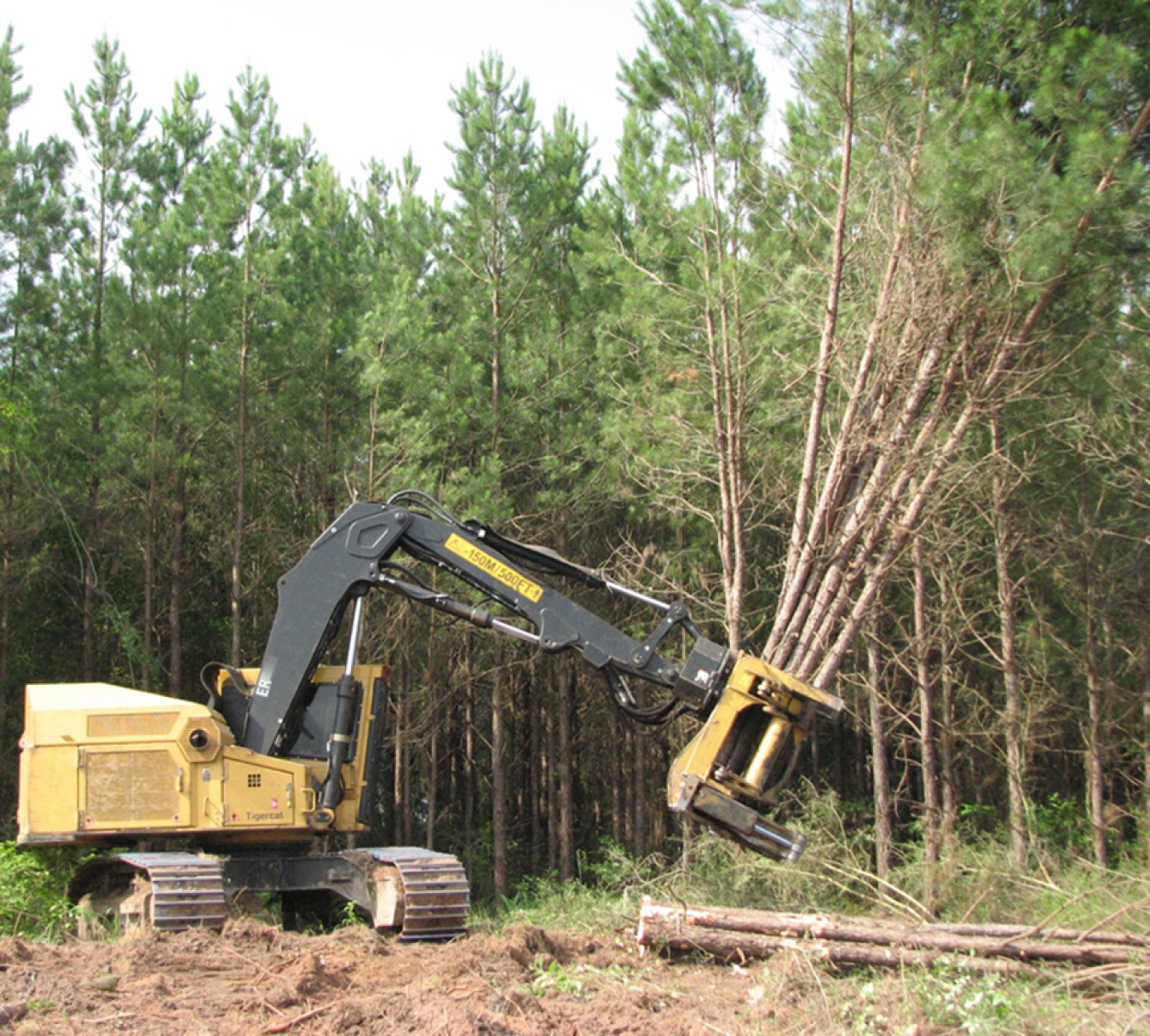
Auburn University Project: Tigercat Tracked Feller Buncher with High-Speed Shear Head
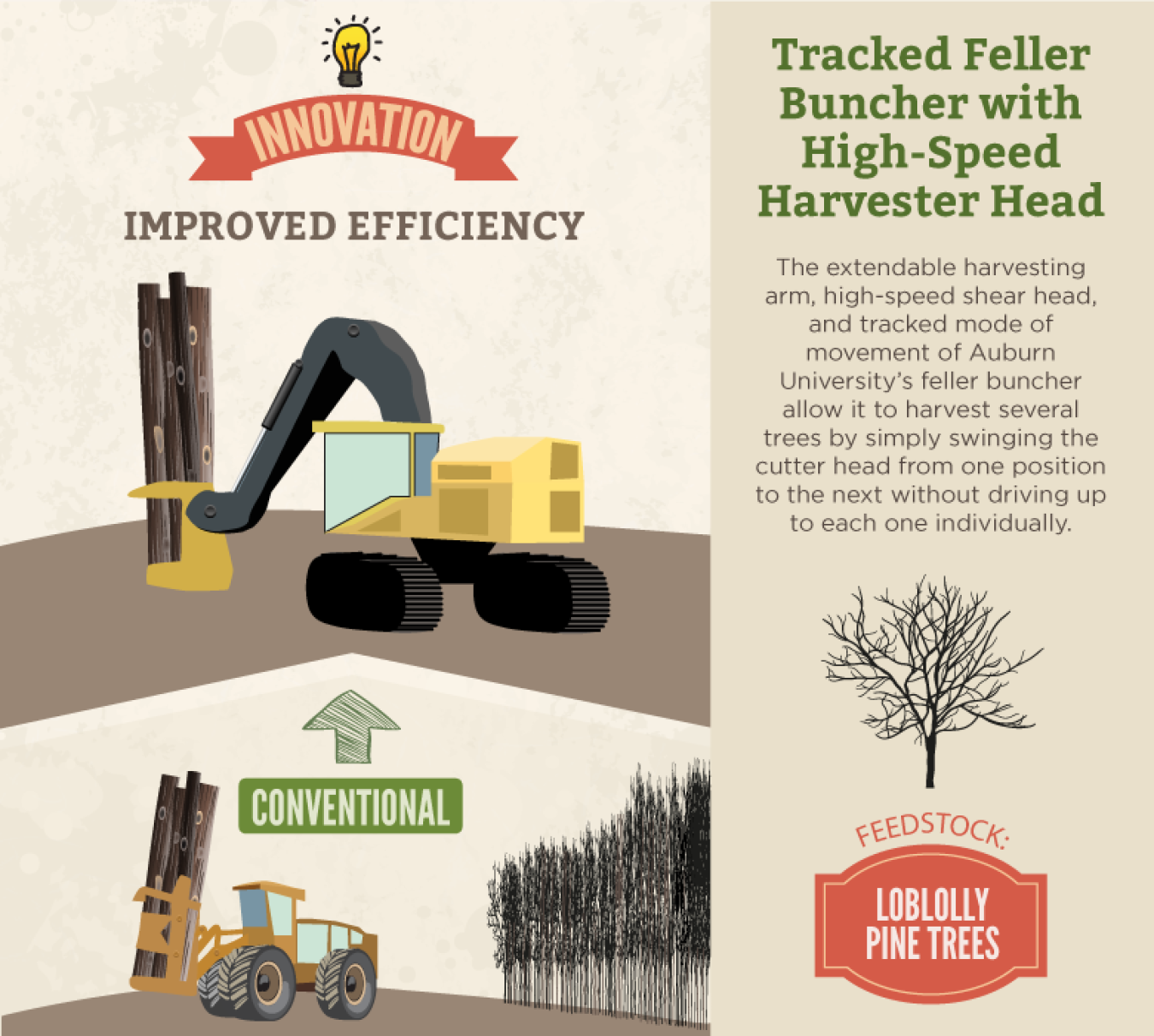
Auburn University’s project included other equipment to be used after felling trees: The Tigercat higher-capacity grapple skids trees out of the forest to a landing; a larger, more efficient grinder makes wood chips; and higher-capacity chip trailers simultaneously maximize weight and volume loads for wood chip transport. See Tigercat’s website for the commercial availability of the equipment.
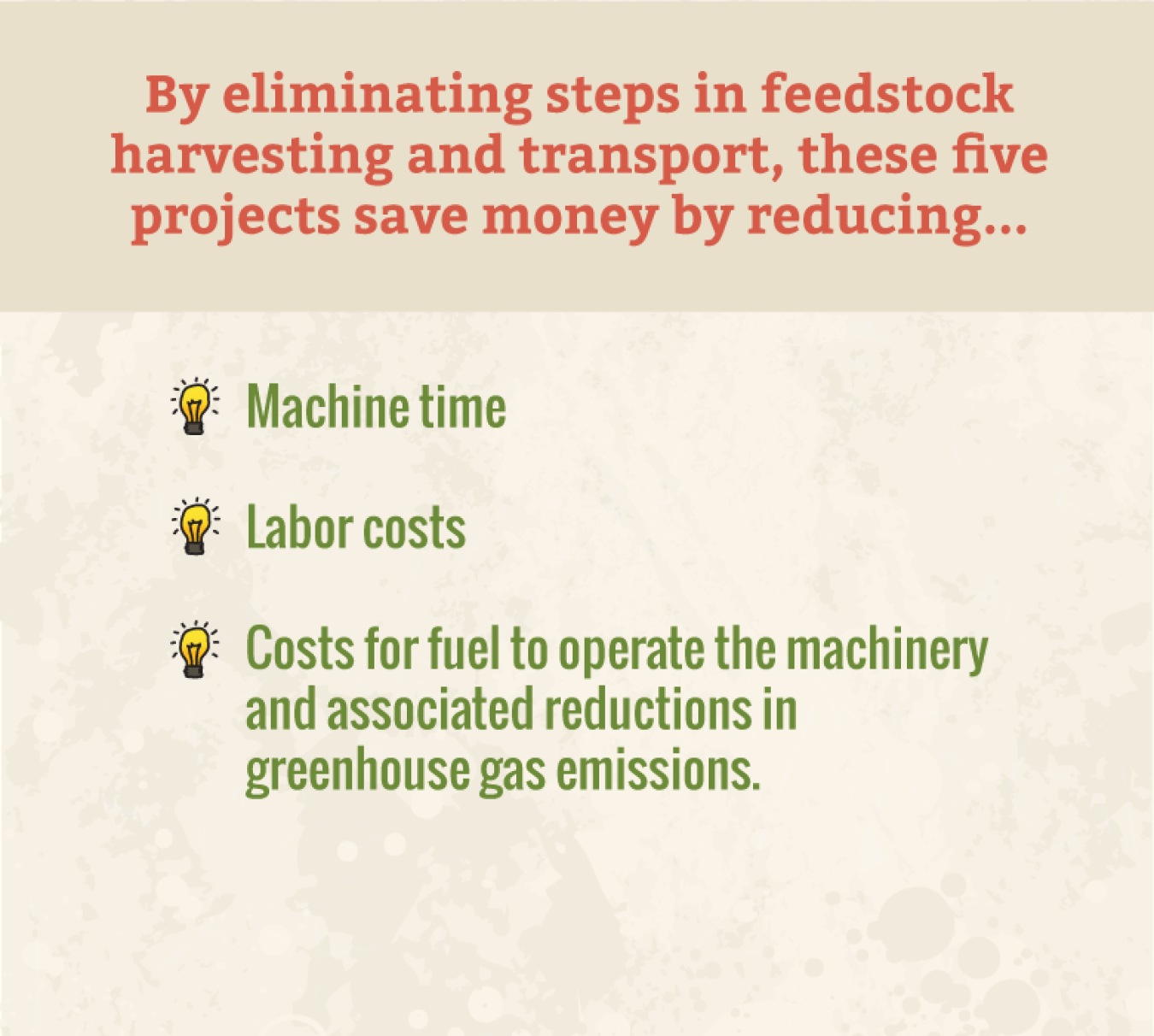
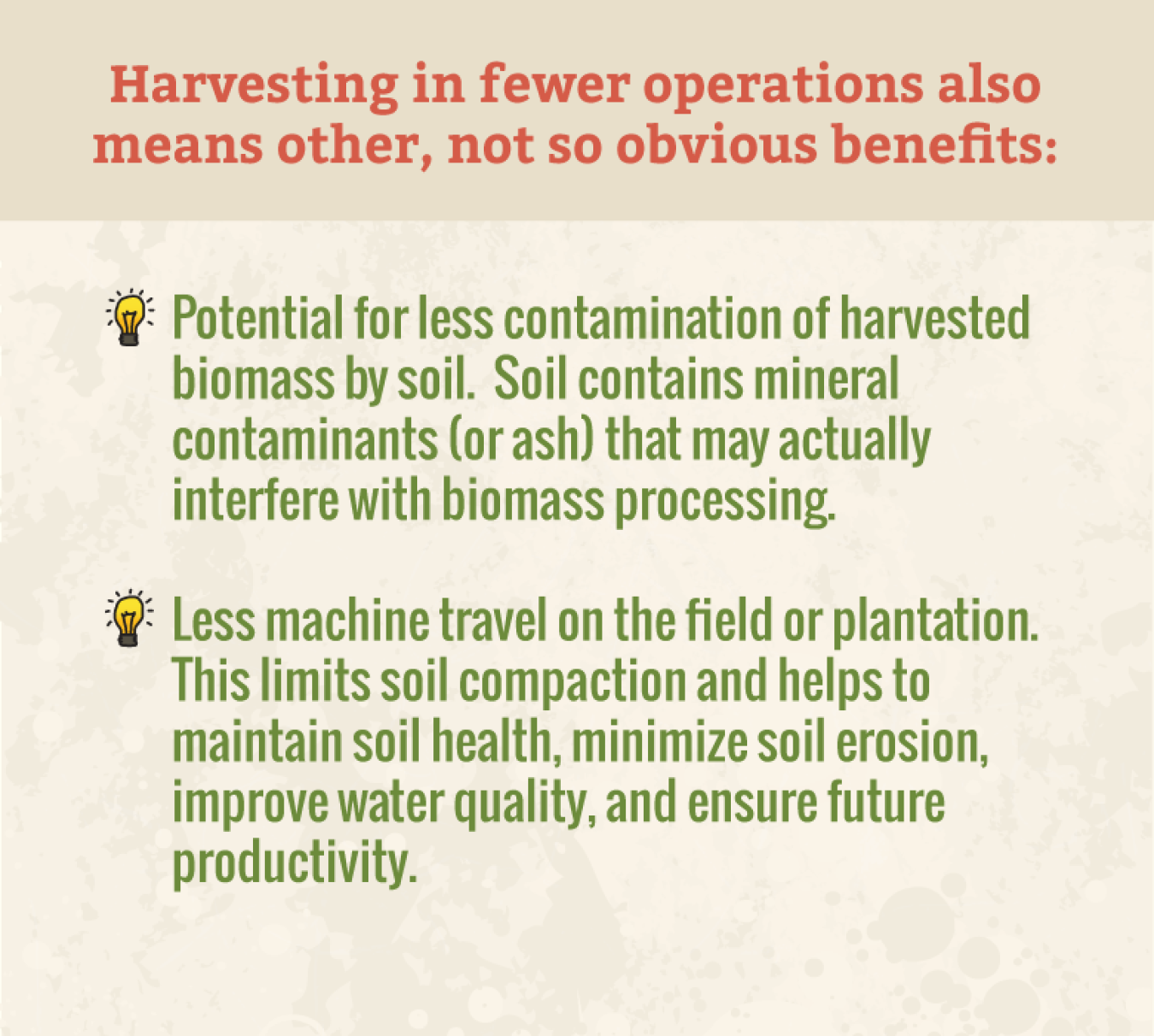
It may look like ordinary farm equipment, but take a second look. This innovative machinery was developed with Energy Department funding to help biofuels become more affordable. Looking more closely at this image and accompanying infographic, you can see that this combination harvester both harvests and bales corn cobs, husks, stalks, and residue all in one step. Its purpose is to save the time and money required to harvest corn stover feedstock for biofuel production, ultimately helping make biofuel from non-food sources cost-competitive with petroleum gasoline.
This combination harvester is just one of many new innovative harvesting technologies that were recently completed through $21 million in 2010 Energy Department funding awarded to AGCO Corporation, FDC Enterprises, TennEra, the State University of New York College of Environmental Science and Forestry (SUNY-ESF), and Auburn University. As with two new feedstock logistics projects selected for funding in late 2014, and another in 2013, the purpose was to lower the costs involved in collecting, storing, and transporting corn stover and other cellulosic feedstocks to the biorefinery.
Some of the new machinery is already available on the commercial market, including Tigercat's feller buncher and skidder, and New Holland’s self-propelled forest harvester. Machinery developed through all the projects have led to unique and innovative technologies to harvest corn stover and energy crop grasses and trees—saving labor and machine costs in the biomass supply chain while reducing greenhouse gas emissions from harvesting and logistics operations. Demonstrations of the projects showed cost reductions of as much as 34% over conventional systems.
Each award recipient was required to partner with at least one biorefinery—such as newly opened POET-DSM’s Project LIBERTY and the Abengoa Bioenergy Biomass of Kansas facility—and with at least one original equipment manufacturer—responsible for designing, building, and demonstrating the equipment. Original equipment manufacturers included Stinger (partnered with AGCO Corporation); Kelderman Manufacturing, Allied-Freeman, Vermeer, and Rotochopper (partnered with FDC Enterprises); Marathon Equipment, Laidig Systems, and Deere & Co. (partnered with TennEra); New Holland (partnered with SUNY-ESF), and Tigercat (partnered with Auburn University). Streamlining steps in the biomass harvesting and delivery process is important because biorefineries can only produce as much biofuel as there is feedstock, and cost reductions create savings that ultimately translate to lower biofuel prices.