Innovative Process and Materials Technologies
Advanced Manufacturing & Industrial Decarbonization
March 31, 2016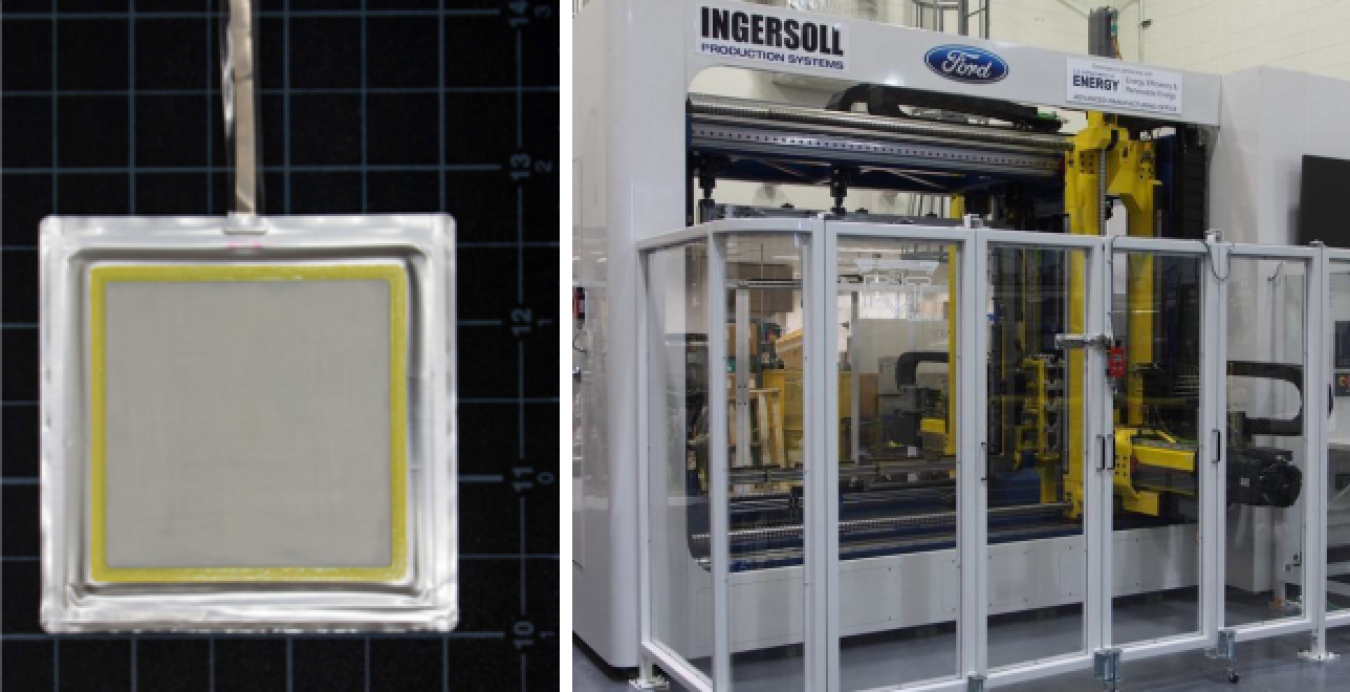
R&D Projects support the development of a wide range of processes and technologies, including (left) development of a manufacturing process for, and commercialization of, advanced Protected Lithium Electrodes (image courtesy of PolyPlus Battery Company); and (right) the design, build, and commissioning of a RApid Freeform sheet metal Forming Technology (RAFFT) that eliminates stamping and forming dies that will enable rapid prototyping for vehicle parts (image courtesy of Ford Motor Company).
INNOVATIVE PROCESS AND MATERIALS
U. S. industry consumes approximately 30 quadrillion Btu (quads) of energy per year, which is almost one third of all energy used in the United States. Solutions that increase energy productivity (output per unit of energy used) within industry are needed to ensure that U.S. producers lead the world in modern production technologies. Innovative manufacturing process technologies and materials can help reinvigorate existing manufacturing industries while supporting the growth and development of clean energy technologies and new industries in the United States.
R&D projects support the development of innovative manufacturing processes and materials technologies to advance the clean energy economy by:
- Increasing industrial and manufacturing energy efficiency
- Delivering the breakthroughs that the nation needs to significantly reduce energy and carbon intensity throughout the economy over the coming decades
- Revitalizing existing manufacturing industries and supporting the development of new products in emerging industries
View the project portfolio and associated fact sheets:
A Novel Flash Ironmaking Process
Advanced, Energy-Efficient Hybrid Membrane System for Industrial Water Reuse
Scale-Up of Novel Low-Cost Carbon Fibers Leading to High-Volume Commercial Launch
Continuous Processing of High Thermal Conductivity Polyethylene Fibers and Sheets
Innovative Manufacturing of Protected Lithium Electrodes for Ultra High Energy Density Batteries
High Metal Removal Rate Process for Machining Difficult Materials
Rapid Freeform Sheet Metal Forming: Technology Development and System Verification
Conversion of Waste CO2 and Shale Gas to High Value Chemicals
No Heat Spray Drying Technology
Novel Membranes and Systems for Industrial and Municipal Water Purification and Reuse
A Novel Unit Operation to Remove Hydrophobic Contaminants
Low-Energy, Low-Cost Production of Ethylene by Low-Temperature Oxidative Coupling of Methane
Coatings and Process Development Reduced Energy Automotive OEM Manufacturing
Low-Cost Bio-Based Carbon Fiber for High Temperature Processing
Energy Efficient Thermoplastic Composite Manufacturing
One Step Hydrogen Generation through Sorption Enhanced Reforming
High Thermal Conductivity Polymer Composites for Low Cost Heat Exchangers
No Heat Spray Drying Technology
Novel Membranes and Systems for Industrial and Municipal Water Purification and Reuse
A Novel Unit Operation to Remove Hydrophobic Contaminants
Low-Energy, Low-Cost Production of Ethylene by Low-Temperature Oxidative Coupling of Methane
Coatings and Process Development Reduced Energy Automotive OEM Manufacturing
Low-Cost Bio-Based Carbon Fiber for High Temperature Processing
Energy Efficient Thermoplastic Composite Manufacturing
One Step Hydrogen Generation through Sorption Enhanced Reforming
High Thermal Conductivity Polymer Composites for Low Cost Heat Exchangers