On Thursday, April 14, hundreds of industry leaders, researchers, and “Maker Community” members converged at the Rayburn House Office building for 3D/DC 2016, one of the nation’s preeminent 3D printing policy events. Hosted by The American Societ...
Advanced Manufacturing & Industrial Decarbonization
April 29, 2016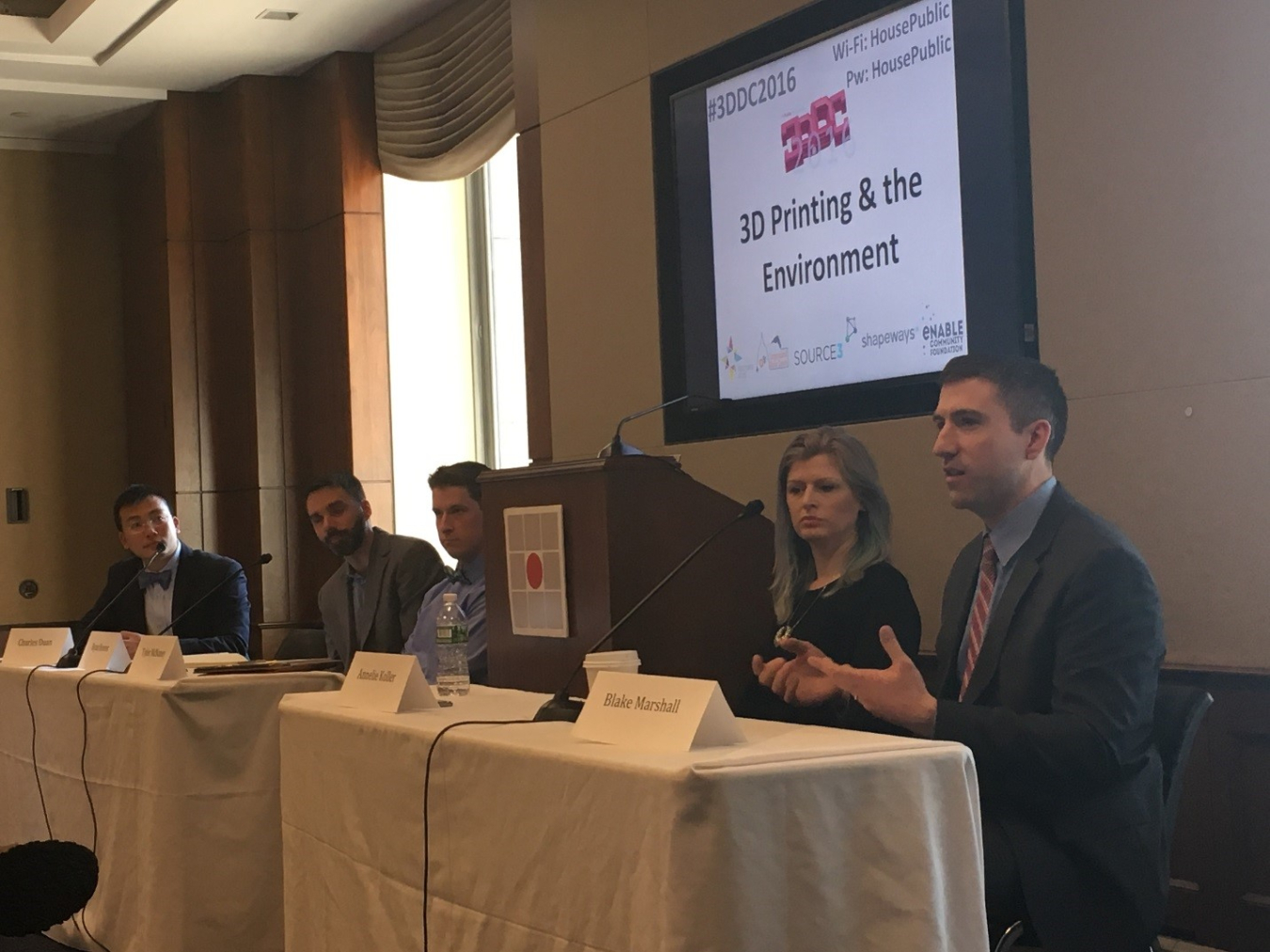
On Thursday, April 14, hundreds of industry leaders, researchers, and “Maker Community” members converged at the Rayburn House Office building for 3D/DC 2016, one of the nation’s preeminent 3D printing policy events. Hosted by The American Society Of Mechanical Engineers (ASME) and Public Knowledge, 3D/DC 2016 featured several panel discussions on topics such as STEAM Education, the Arts, the Environment, Bridging the Workforce Skills Gap, and Social Impact. Blake Marshall, a physical scientist and technology manager for the Advanced Manufacturing Office (AMO), served as a panelist for the 3D Printing and the Environment panel. Blake manages research and development programs that advance the state of the art in additive manufacturing technologies for the AMO. He engaged with a diverse group of participants and highlighted some of AMO’s activities in 3D printing research and development. A major focus of the environment panel was the positive impact that 3D printing could have on the environment and the importance of developing recyclable feedstocks for additive manufacturing to further increase sustainability.
Many of the additive manufacturing projects that AMO supports demonstrate the cross-cutting value of the 3D printing technology and applications across various sectors. AMO has teamed with other program offices in revolutionary projects including:
- The Additive Manufacturing Integrated Energy (AMIE) project, a collaborative effort sponsored by DOE’s Building Technologies Office (BTO), Vehicle Technologies Office (VTO), and AMO, created a 3D printed house and vehicle that share an integrated energy system. This project demonstrated rapid prototyping using 3D printing and a revolutionary new energy integration system.
- AMO has also teamed up with the Wind and Water Power Technologies Office (WWPTO) to apply 3D printing to the manufacture of wind turbine blade molds, an innovative approach that could reduce cost and time associated with manufacturing, experiment with new capabilities, and improve design flexibility.
These projects show that 3D printing cannot only revolutionize the manufacturing industry, but it can also be applied to the manufacture of clean energy technologies. To learn more about AMO’s investments in technologies to make manufacturing cleaner and more efficient, click here.
To view the full 3D Printing and the Environment panel video, click here.