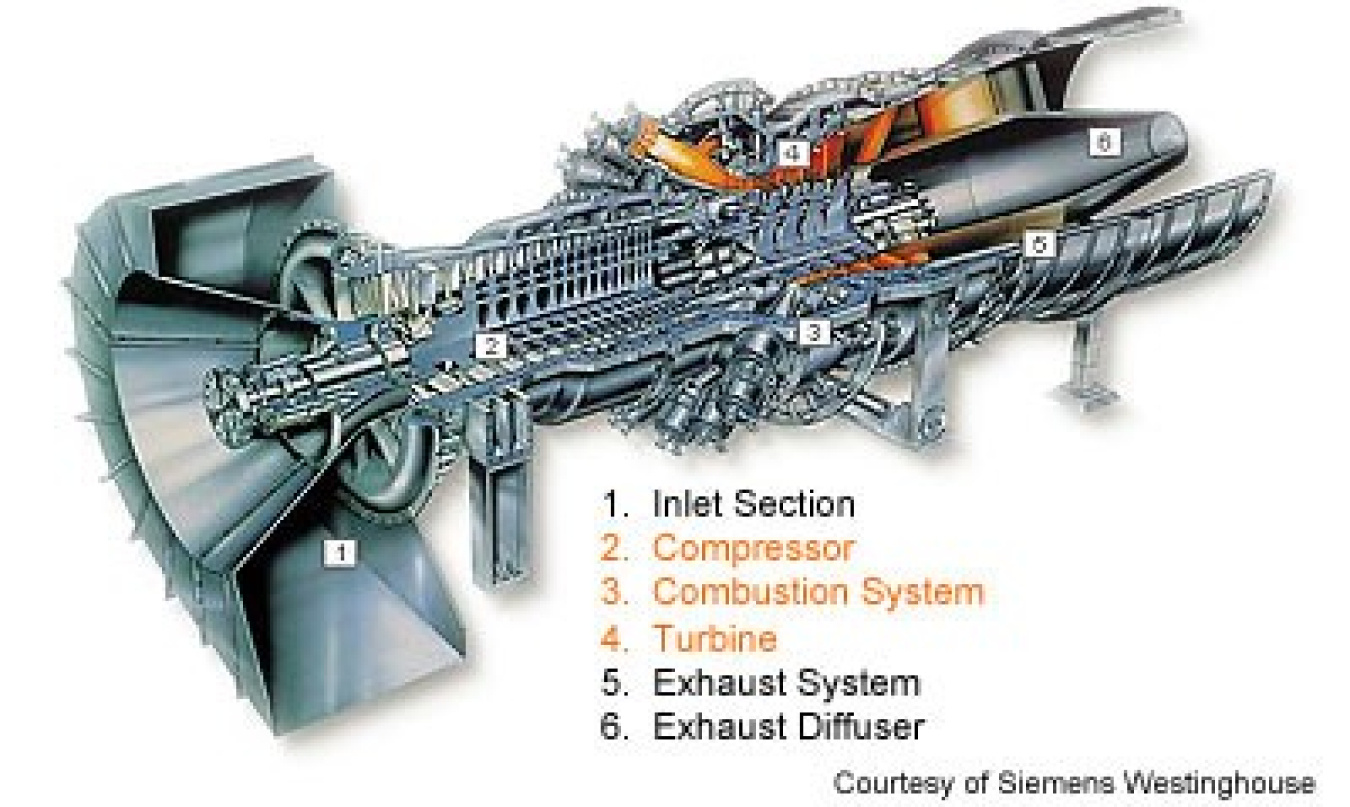
Combustion (gas) turbines are key components of advanced systems designed for new electric power plants in the United States. With gas turbines, power plants will supply clean, increasingly fuel-efficient, and relatively low-cost energy.
Advanced turbine based cycles like supercritical CO2-based (sCO2) power cycles have shown the potential for increased heat-to-electricity conversion efficiencies, high power density, and simplicity of operation compared to existing steam-based power cycles. The sCO2 power cycle utilizes small turbomachinery, is fuel- and/or heat-source neutral, and efficient.
The U.S. DOE continues its efforts to push the limits of turbine performance in response to the nation’s increasing power supply challenges by focusing on the underlying factors affecting combustion, aerodynamics/heat transfer, and materials for advanced turbines and turbine based power cycles. Temperature continues to be the barrier for increasing turbine efficiency. Research being pursued by the program will enable turbines to operate in excess of 3100°F, with low NOx emissions, increased power output, and efficiencies over 65%. Some of the technologies that will enable this transformational jump in capabilities include ceramic matrix composites (CMCs) for airfoils and combustion components, advanced low-NOx micro-mixer combustion system that can efficiently fire multiple fuels at different loads while keeping emissions low, and pressure gain combustion. Pressure gain combustion is an alternate form of combustion that increases pressure through the combustor compared to standard combustion techniques that result in a pressure loss. Integrating this technology into a combustion turbine could provide further performance increases.
Supercritical CO2 power cycles using advanced turbomachinery could offer efficiency and performance improvements for some fossil energy cycles. The turbines for these cycles are unique in that they will have high power density, lower peripheral speeds, high blade loading, and high shaft speeds, all of which will factor into the final turbine designs. The high pressure, relatively high temperature, uncertainty of the CO2 state near the critical point, and high power density create design challenges for the supercritical CO2 turbomachinery.
Advanced Ultrasupercritical (AUSC) power cycles offer efficiency and performance improvements for steam turbines operating above 700°C and 220 bar main steam temperature and pressure. Steam turbine designs for these cycles and higher will have turbomachinery challenges related to materials of construction, shaft end seals, turbine blade seals, and turbine control/bypass valves.
NETL Involvement
The Advanced Turbine program supports projects for developing new technologies that can be deployed by industry for new builds and adapted to the existing fleet, and it catalyzes a knowledge base for the domestic OEMs of combustion and steam turbines.
The National Energy Technology Laboratory (NETL) supports advanced combustion turbine technology such as pressure gain combustion, innovative cooling designs, advanced materials, and combustion systems for firing hydrogen or blends of hydrogen and natural gas. More information on the Advanced Turbine program can be found here.
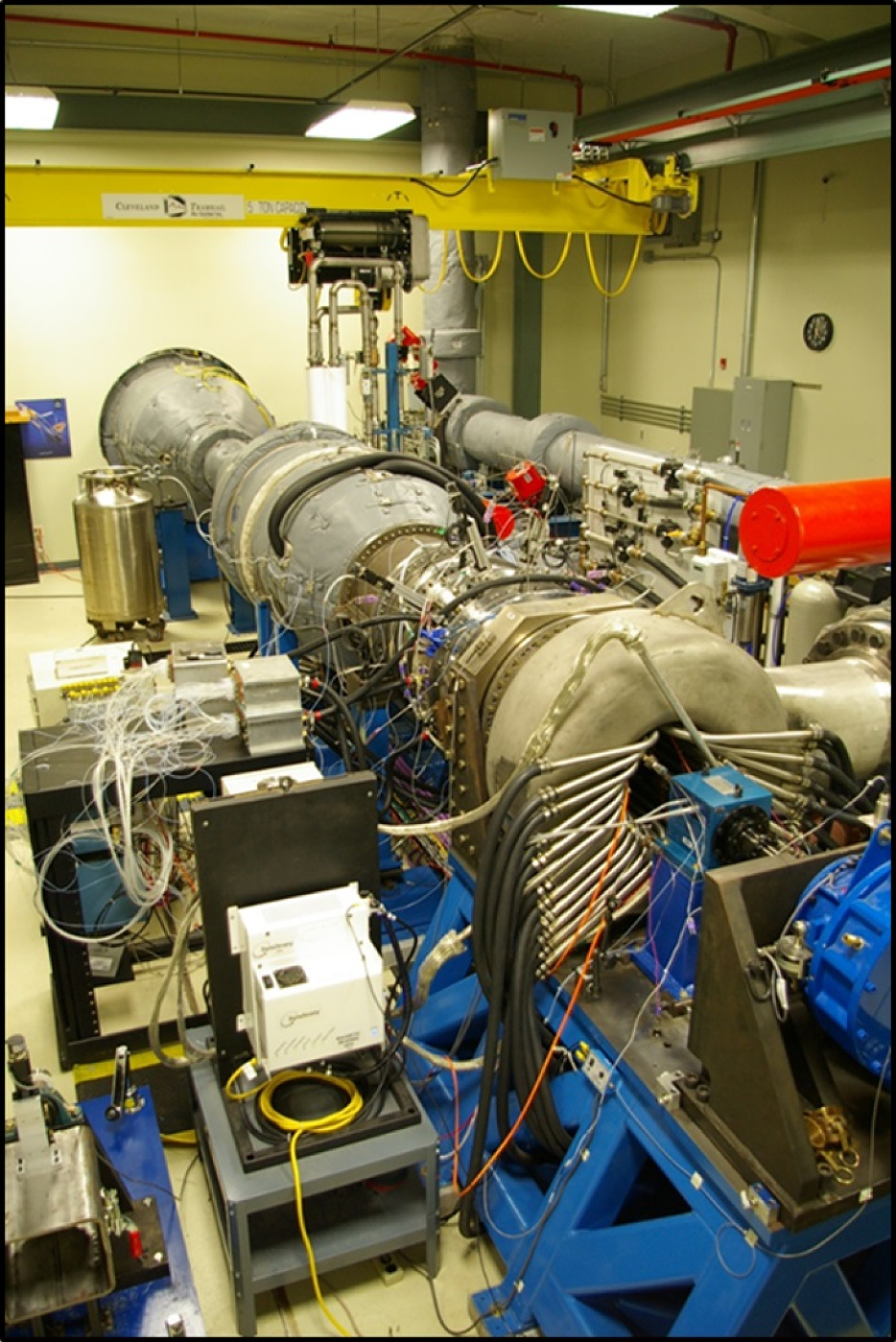
NETL supports the development of sCO2 technology, including the Supercritical Transformational Electric Power (STEP) program, which includes the design, construction, and operation of a 10 MWe pilot scale sCO2 facility. DOE is working with partners such as the Gas Technology Institute, Echogen Power Systems, Southwest Research Institute, and General Electric to develop and mature the technology at the pilot scale. The program goals are to facilitate the commercialization of sCO2 Brayton Cycles and spur the development of necessary designs, materials, components, operation and control systems, sensors, understanding, and characterization needed for larger scale sCO2 power conversion systems. More information on sCO2 and STEP can be found here.
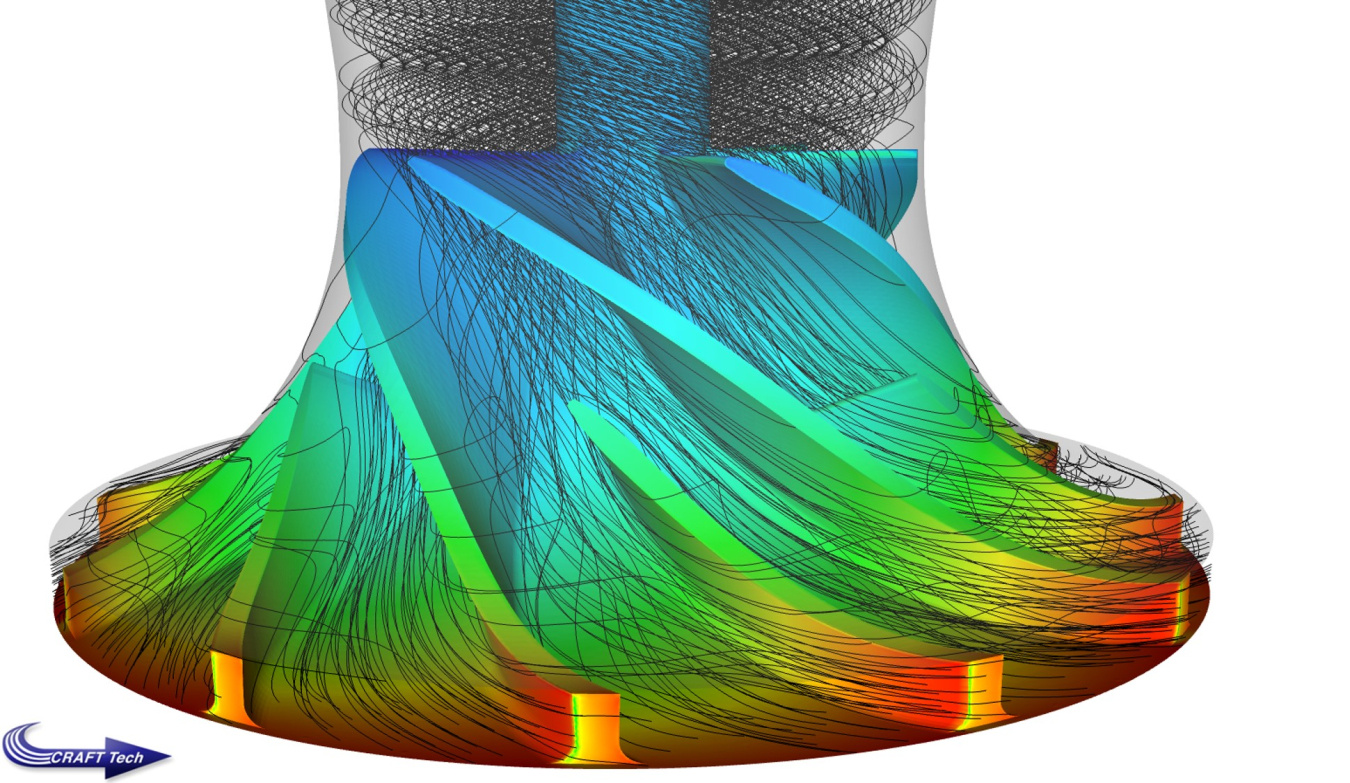
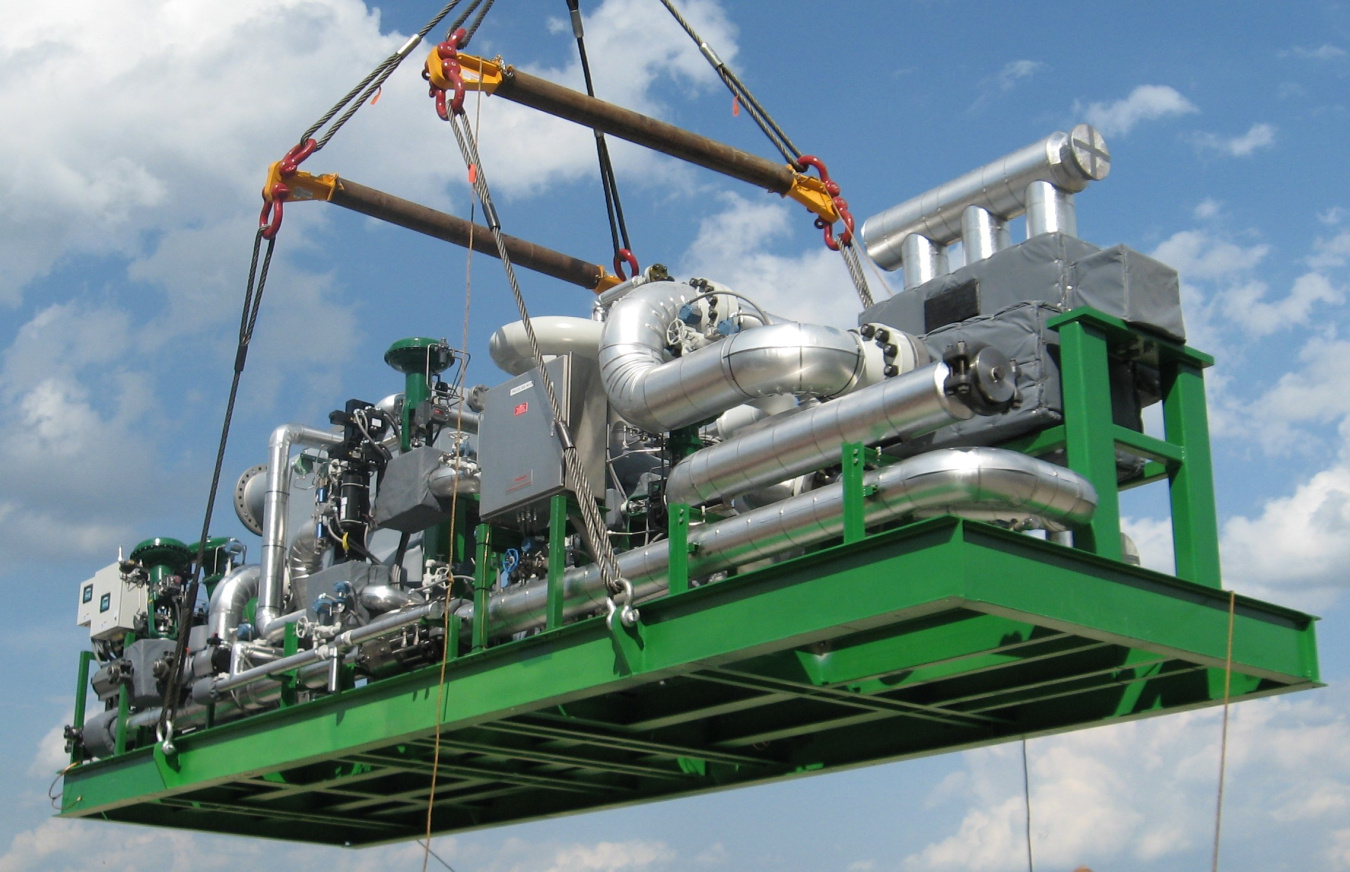