Researchers at the Department of Energy’s National Energy Technology Laboratory (NETL) believe copper may play an important role in combatting climate change. When used as a part of a promising coal combustion technology known as chemical looping, co...
Office of Fossil Energy and Carbon Management
February 18, 2016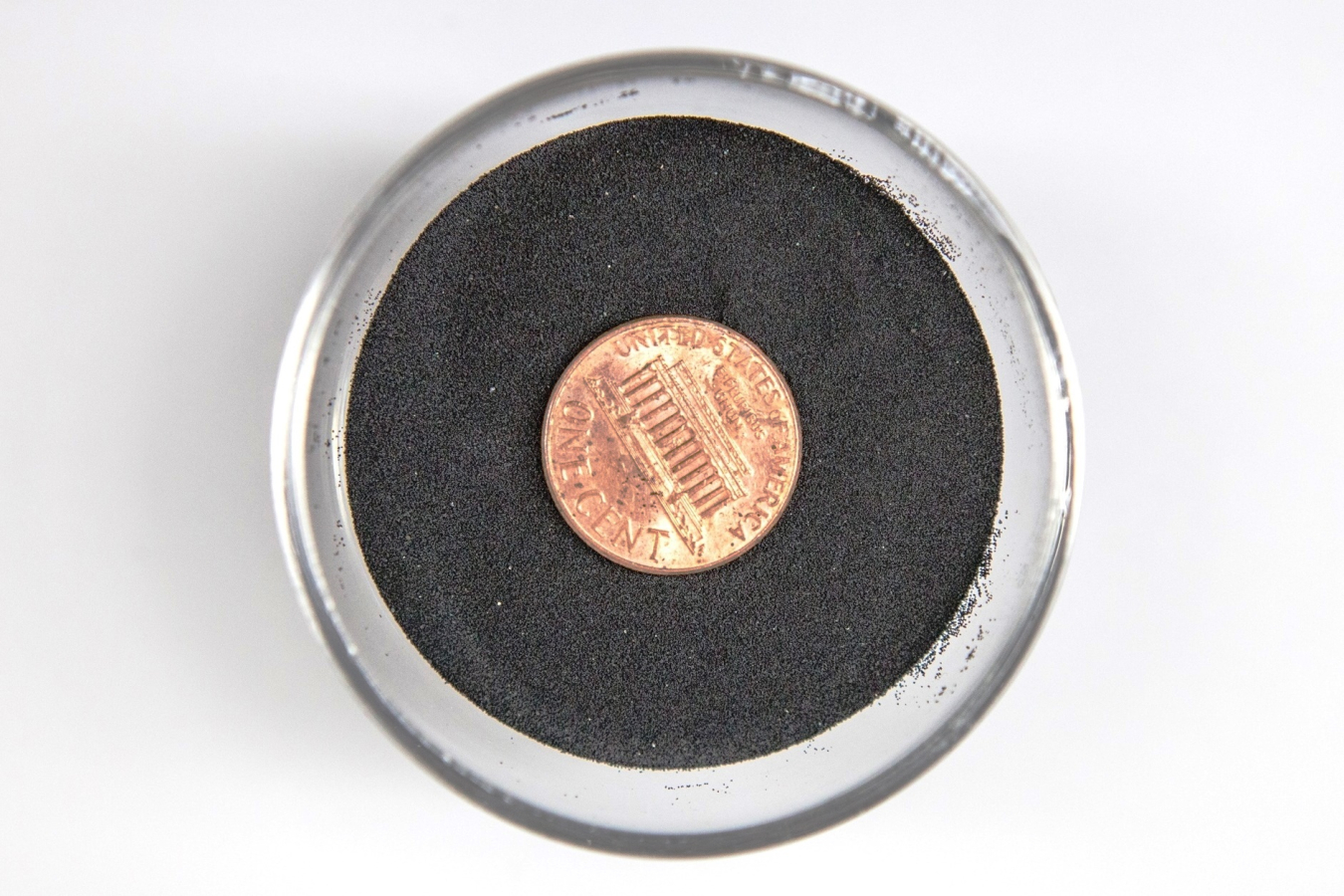
Copper. It’s been used in wires, pipes, and pennies for decades. Ancient Egyptians used it to sterilize wounds and clean drinking water. Today some hospitals are using it to reduce bacterial infections.
Now, researchers at the Department of Energy’s National Energy Technology Laboratory (NETL) believe copper may play an important role in combatting climate change. When used as a part of a promising coal combustion technology known as chemical looping, copper can help economically remove carbon dioxide (CO2) from fossil fuel emissions.
In traditional power plants, coal is pulverized and then burned in air to create the steam that powers electricity-producing turbines. In chemical looping, the fuel (pulverized coal or natural gas) is combusted through reaction with oxygen-bearing materials like iron oxide, called oxygen carriers. After combustion, the oxygen-depleted carrier is circulated to an air reactor, where it is again oxidized, in preparation for transport back to the fuel reactor to begin a new coal-burning cycle. In some ways, the process is similar to how blood circulates through our bodies, carrying oxygen to the heart and out to the muscles, and then looping back to the heart again to get new oxygen.
One of the advantages of chemical looping is that the process produces a nearly pure exhaust stream of CO2 that can be easily captured without expending the additional energy usually required for separating gas streams. The CO2 can then be used to produce other products, or it can be permanently stored underground. The chemical looping process can also help reduce emissions of smog-causing nitrogen oxides.
But for chemical looping to become a widespread commercial reality, we have to find more efficient oxygen carriers. That’s where copper comes in. When copper is used as a key ingredient in oxygen carriers, it appears to improve the efficiency of chemical looping.
NETL’s Ranjani Siriwardane explained that preliminary testing of a new copper-based oxygen carrier has shown outstanding potential. “In our tests, a copper-based oxygen carrier was prepared and used in the chemical looping process,” she said. “It showed good solid circulation, good methane conversion and good heat management.”
The possibility of using copper as an oxygen carrier has always been limited by copper’s low melting point. This has caused copper-containing carriers to accumulate or stick together at high temperatures—known as agglomeration—which reduces effectiveness of the process.
Siriwardane said the NETL breakthrough came when researchers were able to design a mixed metal oxygen carrier containing iron oxide and a high concentration of copper oxide to create a highly reactive oxygen carrier that can withstand high temperatures, eliminating agglomeration problems.
Tests on the oxygen carrier were conducted in a pilot scale chemical looping combustor unit at NETL. And the results were promising. “We conducted the tests at around 800 and 900°C. What we found was the design we developed can function in a chemical looping reactor more efficiently than traditional oxygen carriers,” Siriwardane said. “It takes us closer to the possibility of deploying chemical looping on a large scale as a less expensive way to reduce CO2 emissions.”
NETL researchers have applied for a patent on the new approach. The next step in its development will be testing at commercial scale.