Foamed cement, which looks and feels like a gritty gray shaving cream, is used during oil and gas drilling operations to encase production tubes and prevent leaks and spills. The cured material creates a seal that protects underground sources of drinki...
Office of Fossil Energy and Carbon Management
September 29, 2016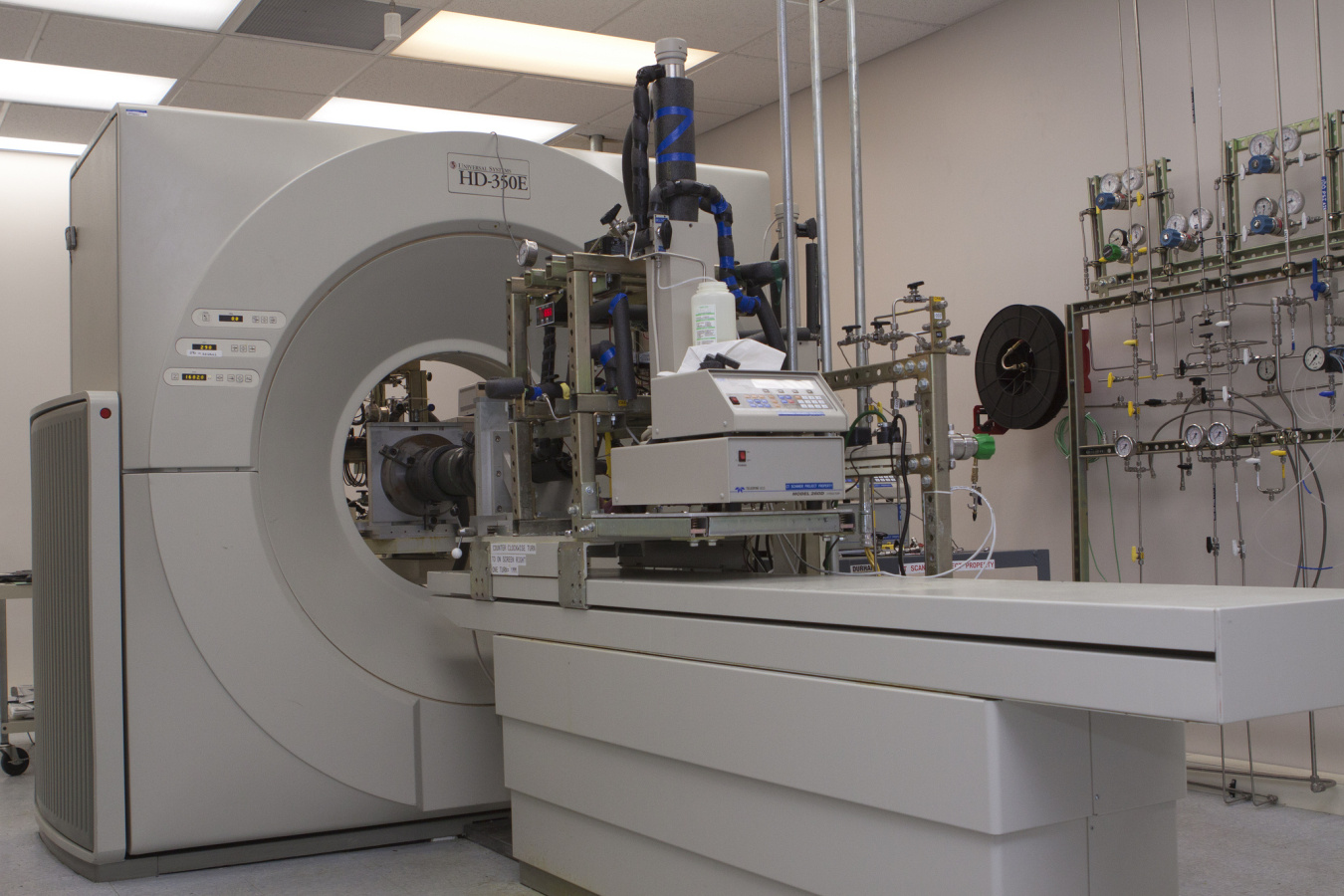
Foamed cement, which looks and feels like a gritty gray shaving cream, is used during oil and gas drilling operations to encase production tubes and prevent leaks and spills. The cured material creates a seal that protects underground sources of drinking water, but this is no ordinary cement.
When foamed cement is mixed, gases like nitrogen are injected into the slurry to create microscopic bubbles. The size and distribution of these bubbles will determine the stability of the cement, so researchers must test samples to assure quality. The American Petroleum Institute (API) developed protocols and testing standards for mixing foamed cement in the lab, but in the field, different machinery is used to mix and pump the cement. So, would these field samples look like those from the laboratory?
NETL worked with API’s Cement Subcommittee 10C to answer that question. Researchers tested field samples using NETL’s multi-scale CT scanning facilities, which are capable of replicating the pressures of a wellbore while peering into the sample. These CT scans provided data on real materials under real conditions, and the results showed that field samples did not look like the laboratory samples.
This research illustrated that the equipment used to generate foamed cement has a major impact on its properties. The data obtained by NETL can now be used by API to correlate lab performance with field behavior and help to rewrite the old standard.
A new testing standard will help ensure quality, reduce cost, decrease waste, and support safer oil and gas operations around the world.