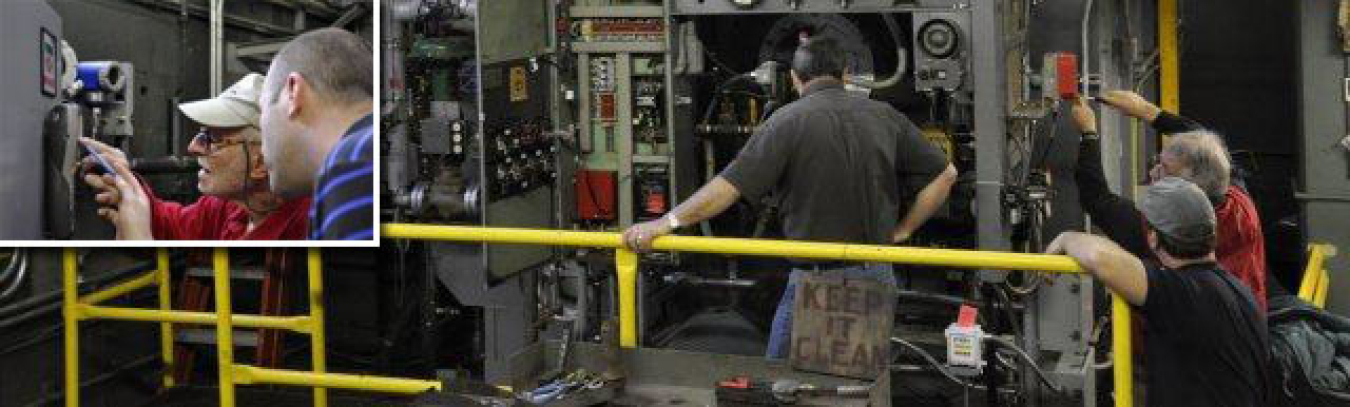
Technical staff are making boiler adjustments with the control and monitoring system. Photo courtesy of the Department of Defense’s Environmental Security Technology Certification Program.
There are more than 45,000 industrial and commercial boilers larger than 10 MMBtu/hr in the United States with a total fuel input capacity of 2.7 million MMBtu/hr. Efficiency of existing boilers can be improved in three ways; replacement with new boilers, replacement of the burner, or installation of a combustion control system. While installation of a new boiler or replacement of the burner can lead to the greatest efficiency gains, the higher costs associated with these measures typically leads to longer payback periods than combustion control systems.
Current combustion-control systems lack continuous carbon monoxide and nitrogen oxide emissions monitoring capability and the automated controls needed to improve fuel performance. This prevents continuous adjustments in the fuel-to-air mixture to maximize efficiency while controlling operation to ensure emissions levels meet regulatory requirements. This new control system enabled continuous monitoring and combustion control and demonstrated improved efficiency and reduced emissions. The demonstrated improvements are better than state-of-the-art combustion control technology, which only 10% of existing boilers use. Most boiler control systems require manual adjustment and have the potential for substantial improvement with automated controls.
Technology Description
A novel combustion control system, along with gas sensors, sets the opening of fuel and air inlets based on flue-gas concentrations. Continuous feedback from measurements of oxygen, carbon monoxide, and nitrogen oxide concentrations enable the control system to improve combustion efficiency while maintaining low carbon monoxide and nitrogen oxide emissions and allows continuous monitoring of boiler performance.
Agency Technology Evaluation Program
The Environmental Security Technology Certification Program (ESTCP) is the Department of Defense's (DOD) demonstration and validation program for environmental and energy technologies. The ESTCP Installation Energy Test Bed was established in 2009 to demonstrate new energy technologies in a real-world, integrated-building environment to reduce risk, overcome barriers to deployment, and facilitate wide-scale commercialization.
What Were the Benefits?
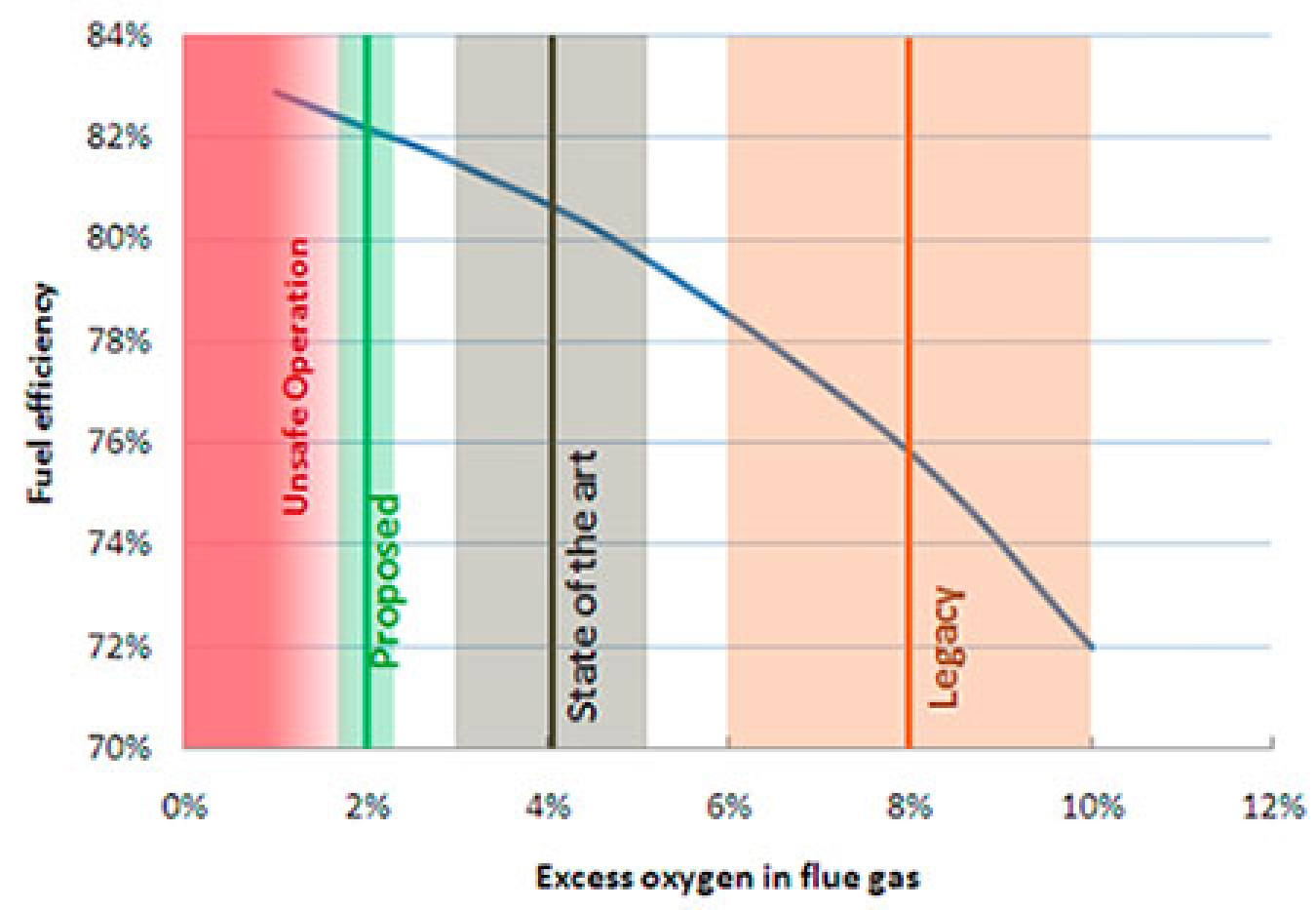
The boiler combustion control and monitoring system was installed on a 25 MMBtu/hr steam boiler located at the Watervliet Arsenal in New York. A one-year test conducted between February 2011 and March 2012 demonstrated a 4% fuel savings for typical utilization with natural gas. The efficiency gain is due to a reduction in oxygen in the flue gas beyond the capability of existing state-of-the-art control systems. Carbon monoxide monitoring ensures that inefficient, potentially unsafe incomplete combustion doesn't occur. This allows very low levels of oxygen in the exhaust flue gas, which improves efficiency. A monitoring and data logging device provides real-time feedback on the boiler performance through a graphical user interface, which enables continuous assessment of the boiler's performance and emissions.
What Were the Savings?
Savings at the Watervliet Arsenal were as follows:
- System operating costs were reduced 3.6% over the baseline and 0.6% over existing state-of-the-art combustion control technology.
- A simple payback of 2.4 years observed for natural gas operation (also associated with lower natural gas prices). For operation with oil, the estimated payback period is 2.5 months.
Potential Applications
The boiler combustion control and emissions monitoring system evaluated has the potential for nationwide application in any hot water or steam boiler using natural gas or No. 2 oil as a fuel and a capacity over 10 MMBtu/hr. The ESTCP study estimated that the boiler combustion control and monitoring retrofit could be deployed broadly, with a large potential for energy savings. According to the study, "the investment in the new technology on a similar boiler burning natural gas would pay back in slightly more than two years with expected fuel savings of $17,000 yearly. When adopted for all 10 to 100 MMBtu/hr boilers older than ten years across DOD, the demonstrated technology has the potential to save $56 million of fuel costs annually, and avoid the emission of 600,000 tons of carbon dioxide."
Summary of Advantages for Boiler Combustion Control and Monitoring System | |||
---|---|---|---|
Improved Efficiency | Emissions Monitoring | Continuous Feedback | Ease of Operation |
The control and monitoring system improved efficiency over existing, state-of-the-art boiler controls. | Carbon monoxide and nitrogen oxide emissions sensors ensure that the boiler's emissions are below regulatory requirements. | The graphical user interface enables continuous assessment of boiler performance. | Boiler operators easily acquired knowledge of controller operation and interface, and were able to operate it and take action. |
Achieving Energy Savings in Your Facility
The project team tested the boiler combustion control system during its prototype stage. The product is in the final stages of development and certification prior to commercialization.