Complexity, customization and cost are three of the most prevalent barriers to technology integration in commercial buildings.
September 29, 2015Complexity, customization, and cost are three of the most prevalent barriers to technology integration in commercial buildings. But last week at EERE Industry Day, we previewed promising solutions to these barriers. New advanced manufacturing offers access to smaller batches of new, innovative technologies, crowdsourced R&D connects stakeholder needs with new product development, and EERE’s National Laboratory Impact Initiative helps identify pathways to connect smart people and difficult problems.
A collaboration between industry, EERE Buildings, Fuel Cell and Advanced Manufacturing Offices, Oak Ridge National Laboratory (ORNL) unveiled the world’s largest 3D printed structure on Wednesday. And, it even has a name, AMIE, short for the Additive Manufacturing and Integrated Energy demonstration project. Not only is this house 3D printed, but ORNL was able to design, engineer and build it (with a little help from friends like General Electric, Skidmore, Owings & Merrill, Alcoa and the University of Tennessee) in nine months.
Yes, you read that correctly. A house was created from idea to finish in nine months. Plus, it’s energy efficient. The envelope is comprised of high-performing glass and vacuum insulated panels with minimal thermal breaks -- AMIE’s 1-inch walls perform at the same efficiency as a traditional 7-inch wall. The house is equipped with a smart control system that matches its internal loads with solar generation and wireless two-way vehicle power/charging.
Brian Lee of Skidmore, Owings & Merrill said that AMIE was meant to invoke thoughts about the future. And it does.
- What if we could innovate on the fly and still bring highly efficient products to match market needs 5X faster at 100X less cost?
- What if we could create a community to share thousands of ideas, couple those ideas with expert knowledge, and then sell them based on documented demand?
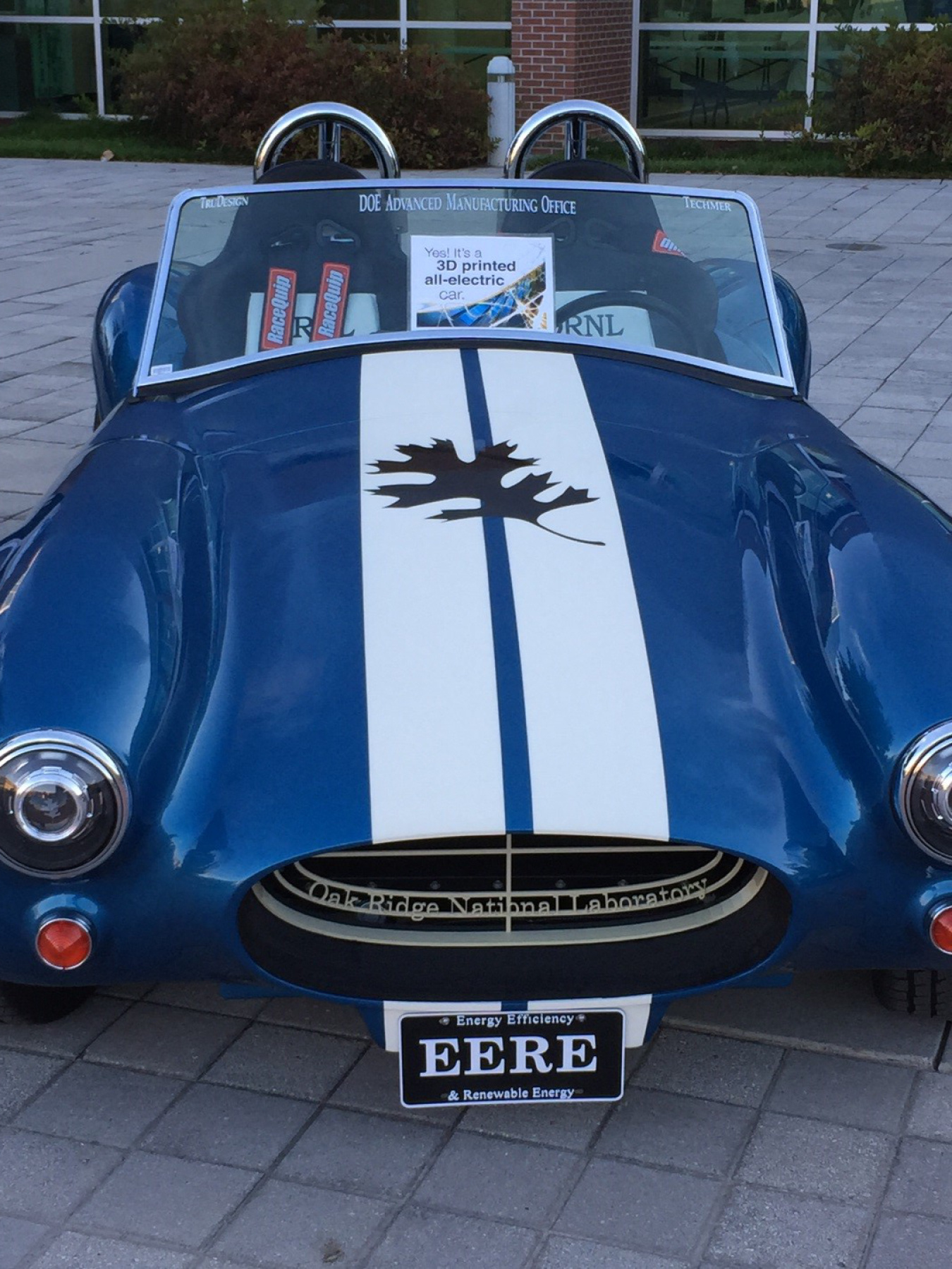
EERE Industry Day answered those questions and recreated a whole new set of “what ifs” for its attendees. Mike Paulus, director of ORNL Tech Transfer, says that if we “invest in smart people solving difficult problems, we as a people will be stronger as a result.”
Jay Rogers of Local Motors showed us the value of this strategy by producing the first 3D printed vehicle (in six months): “made locally, designed by the world with great science and technology.” This is the next iteration of Local Motors work, an all-electric Cobra, printed in six weeks at ORNL’s Manufacturing Demonstration Facility. Yes, it drives. It drives to places like the Detroit Auto Show.
Up next and particularly relevant for those of us in the commercial building community, Local Motors and GE’s 1B FirstBuild are pushing forward to with a focus on appliances. Together they produced a home ice nugget maker -- designed in three months, micro-manufactured in one month, with 6,000 units sold in one month.
Industry Day was a showcase of the best current outcomes of technology R&D and created a new pathway to match those outcomes with market enablers, i.e. listening to consumers and making things that they need and will buy.
At Industry Day we saw the benefits of big data, broad thinking and short timeframes; moving forward, we would like to hear about the best ways that we, the commercial buildings community, can take advantage of this new way of thinking about technology research, development and deployment. Ultimately, when we work together, we can do big things. We can turn those “what ifs” into “we can.”
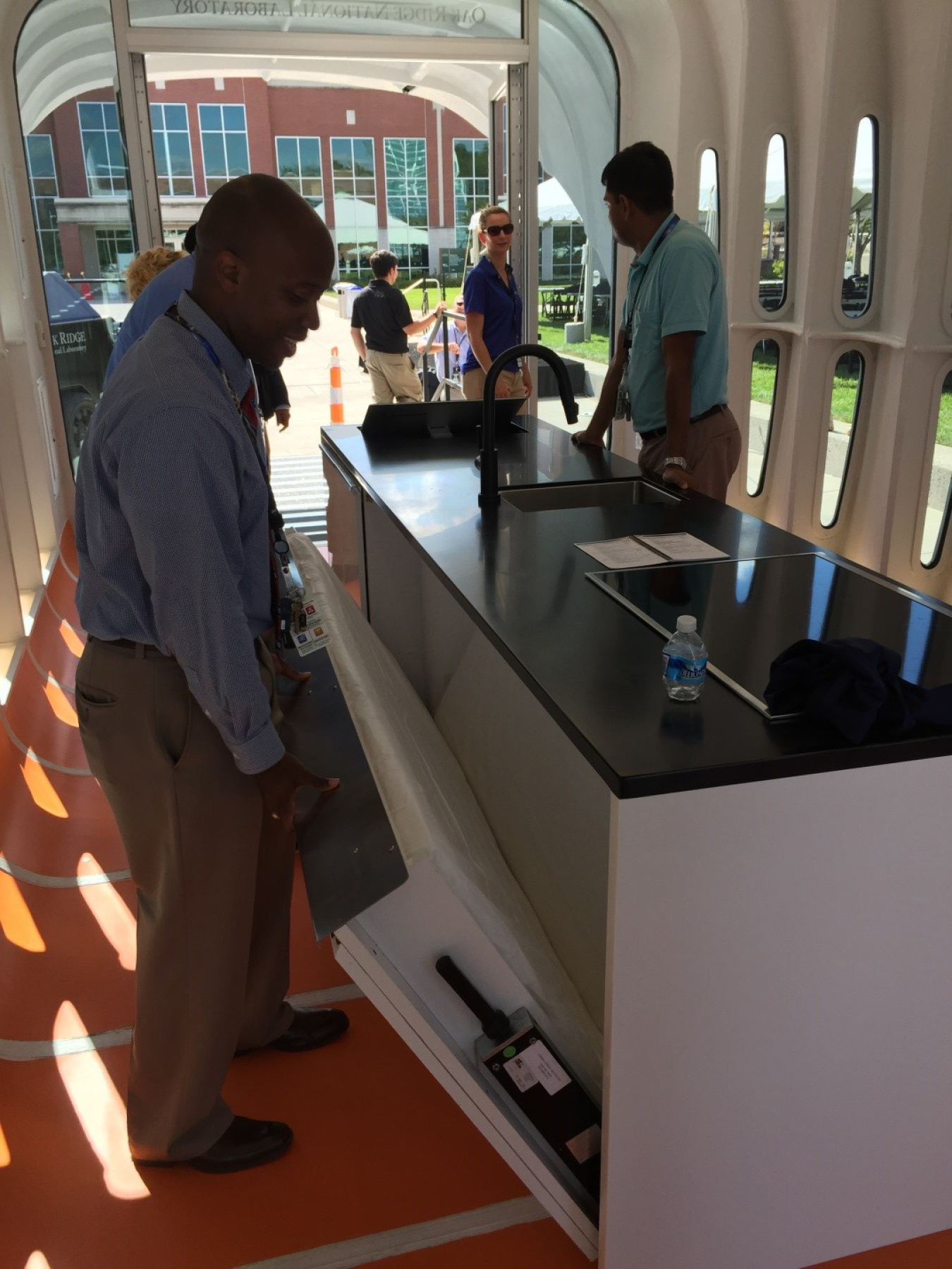
This is Industry Day MVP Rodrick Jackson showing us GE’s micro-kitchen, designed and manufactured for AMIE complete with stove, dishwasher, microwave, refrigerator, sink, and bed.
Let us know what you think: commercialbuildings@ee.doe.gov.