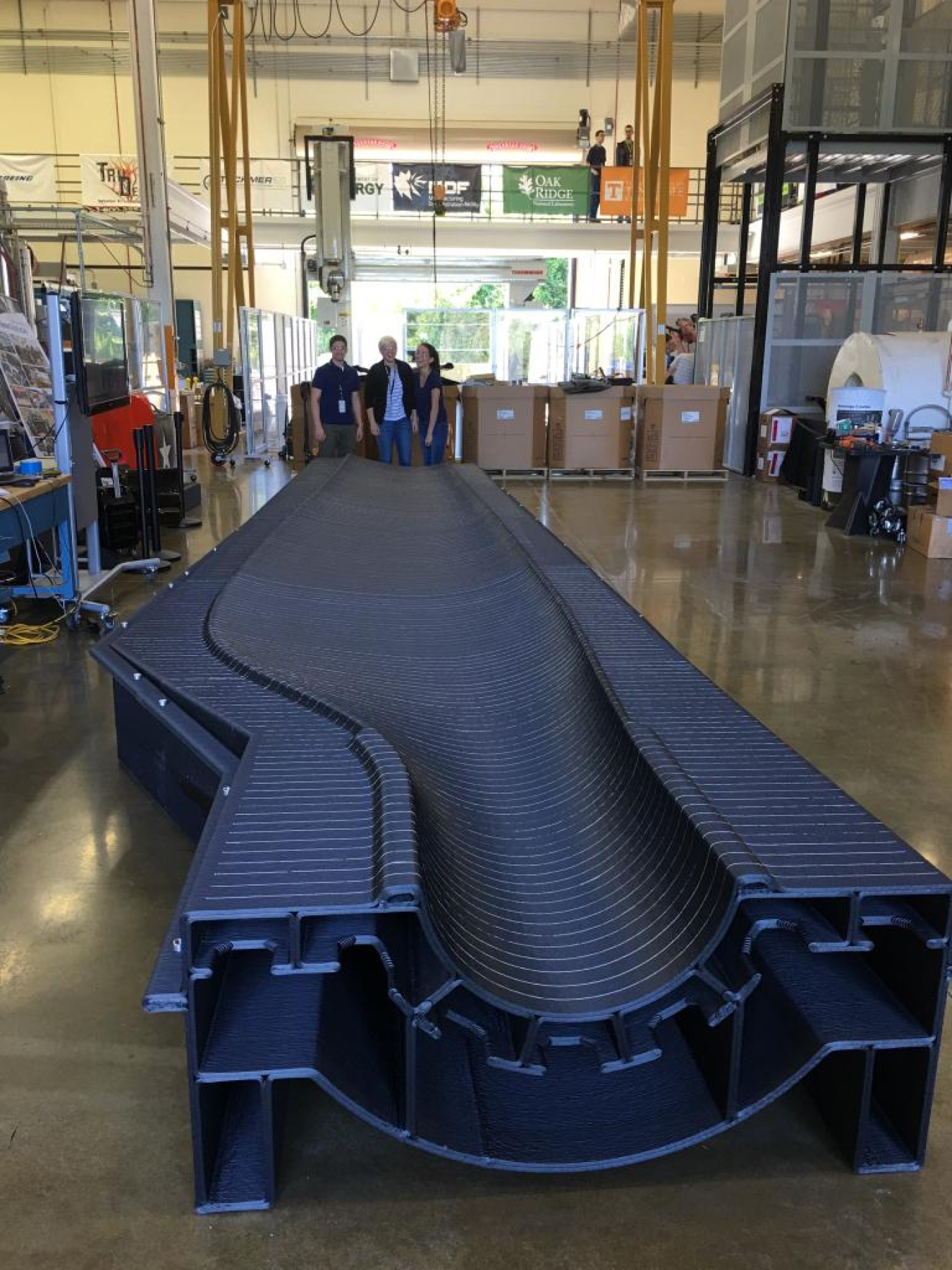
Global Wind Day is a worldwide event that occurs annually on June 15 and is dedicated to discovering the possibilities wind holds to reshape our energy systems. This day provides an opportunity for the Advanced Manufacturing Office (AMO) to highlight work we’re doing in partnership with the Wind and Water Power Technologies Office (WWPTO) to support the development of innovative new manufacturing methods for wind power components. Earlier this year we announced an exciting partnership that applies additive manufacturing, more commonly known as 3D printing, to the manufacture of wind turbine blade molds. We teamed up with DOE’s Wind and Water Power Technologies Office (WWPTO) and joined forces with DOE’s Oak Ridge National Laboratory, Sandia National Laboratory, and corporate partner, TPI Composites on this project to reduce the cost and energy required to manufacture wind power generation components and increase our nation’s competitiveness through manufacturing clean energy technologies. Advancements in 3D printing have made it a valuable tool for reducing waste, decreasing lead time, and offering more flexibility in design. 3D printing systems have also grown in size and capabilities as technology has improved.
The mold for making the blades is being printed using the Big Area Additive Manufacturing (BAAM) machine at the Manufacturing Demonstration Facility (MDF) at Oak Ridge National Laboratory. BAAM is 500 to 1,000 times faster and capable of printing polymer components 10 times larger than today’s industrial additive manufacturing machines. Since the molds will be used to create research blades measuring 13 meters (42 feet) in length, BAAM provides the necessary scale and foundation for this ground-breaking advancement in blade research and manufacturing.
The wind blade mold is first designed using computer-aided design (CAD). Designers begin with a CAD file of the final blade shape and use it to produce the mold which is optimized for 3D printing. Additional features can be added such as assembly holes and heating air ductwork. BAAM then extrudes composite material following the CAD file, printing mold sections up to six feet tall. Once each of the mold sections is complete, a layer of fiberglass laminate is applied to the mold to create a surface compatible with traditional blade-making processes. The fiberglass is machined to achieve the desired shape and surface quality. Each mold segment is then installed on a frame and outfitted with a hot air blower, temperature controller, and thermocouples. This innovative air heating technique saves energy and eliminates the labor-intensive step of hand-laying heating wires which would traditionally be embedded in the mold. The air blowers are also reusable for future molds. Once the frames and air blowers are installed, the blade segments are assembled together and the surface between the segments is patched together to ensure an even, smooth, and vacuum-tight surface. The completed mold is compatible with traditional blade manufacturing methods from this point on.
Since the original announcement of this project, we’ve successfully printed, tested, and assembled mold sections. A sample section of a 3D printed mold and a piece of the wind blade made from the mold were displayed last month at the AWEA WINDPOWER Conference in New Orleans.
Want to see the sample mold and blade section in person? Check us out at the National Maker Faire on June 18-19, 2016 at Booth 57679.